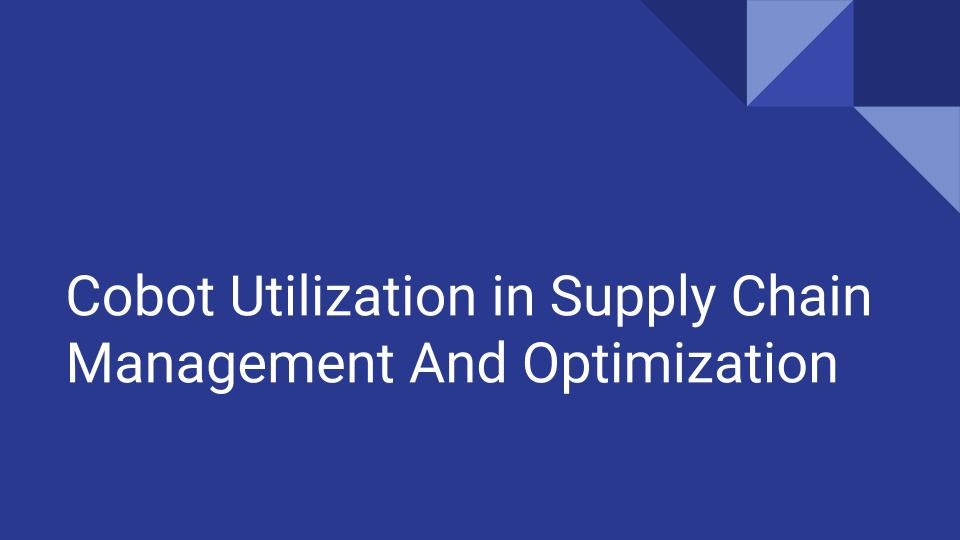
Industry 4.0 is the industrial revolution that all industrialists have been waiting for. As a tool that will optimize and transform the supply chain, organizations that know how to utilize their systems will be the ones who will benefit from the utilization of the technology in order to keep the production process in operation regardless of external operating conditions.
Academic research has identified that collaborative teams of robots with human colleagues are a synergistic fusion. The Cobot revolution is one that we should embrace, instead of fear as productivity is increased by up to 85% in the right circumstances. As the pandemic unfolds, the industrial spend on robotics will continue to escalate over the next few decades.
Cobots are an advancing robotic species, and they do have clear advantages compared to their predecessors. The preceding robots, much like the mainframe computers that preceded laptops, were quite bulky, expensive machines.Innovation is a continuous process, and today we have successfully managed to create advanced robotic systems that are helping people everywhere. Even on the International Space Station, the scientists and engineers onboard the unit are utilizing tools like the Canada Arm to enable them to conduct critical mission activities.
As the intelligence of cobots keeps advancing, the ability to program them to perform functions that are repetitive to humans will be facilitated. Robots now do things like build cars on a continuous basis. Organizations like Tesla employ their robots to do everything from install their sunroofs to paint the car body after the electrolytic treatment process. The high quality and high throughput nature of robots are attributes that are the advantages of these machines. With the ability to program the velocity, direction and distance of motion in a predetermined coordinate grid, the precision of robots is continuing to increase. Supply chain scale up, is definitely a possibility.
While traditional robots have evolved and have started to dominate the market, there is always room for improvement, until we attain the status of lights out manufacturing. Collaborative machines are actually increasing in their production levels over time. The current pandemic is inducing the conditions that will inspire the change.
The Advantages of Cobots
Cobots are very small, organized units. They are designed to be safer, more affordable than traditional robots, and also are adaptable to different tasks. Because of their versatility, they are able to perform tasks in a multitude of environments. Many small and medium-sized organizations are the perfect candidates for the utilization of cobots.
With sensor technology improving in cost efficiency, cobots are now able to be made smarter with each iteration. When it comes to movement, they have sensor perception that allows them to detect humans, and adjust their positions in order to avoid collisions. As easy to train mechanisms, machine learning is one of those underlying principles that enables the units to increase their knowledge. Additionally, with the ability to learn, the units can always be redeployed to different sections in the plant, as they are needed.
This versatility in function, has enabled that by 2025, the market value of cobots will have increased up to $9 billion dollars in value. The cobot industrial market is one that is likely to be one of the fastest growing markets in the robotics space. In 2020, it will be one of the best investments you can make, especially in a time of increased social distancing.
It is safe to integrate Cobots
The current mindset of industry is embracing cobots. The minds of men hold many fears, and COVID-19 has proven that cobots will be the tools that will keep the organization alive. If a pandemic were to cause more humans to have to stay at home, then incorporating a cobot system will enable the digital twins of the humans to actually carry out the much needed tasks. In some dangerous environments, the human can actually be kept safe.
There is also a shortage of highly skilled workers in the technical fields, and with the ability to program a cobot, the gaps can easily be filled by the machines. Employees will feel empowered in the process, as they’ll find that the robots are colleagues. Organizations such as Amazon, have proven that cobots are the key to a successful logistical future. At the Amazon fulfilment centers, there are a series of warehouse based robots that are able to assist with order placement. In some instances, from a civilian perspective, you may have ordered a product, only to find that it has been delivered ahead of schedule. This gain was probably influenced by a cobot. When orders are placed, the cobots actually collect the items for preparation for shipment.
Via a sensor network embedded into the employees clothing, the cobots can sense human presence and the two are able to navigate around the factory in a seamless fashion. The cobots actually respect humans, and will reduce their activity in the presence of a human.
Company employees continue to be trained in the process, but the Amazon case study is definitely a win-win situation for the staff and the robots.