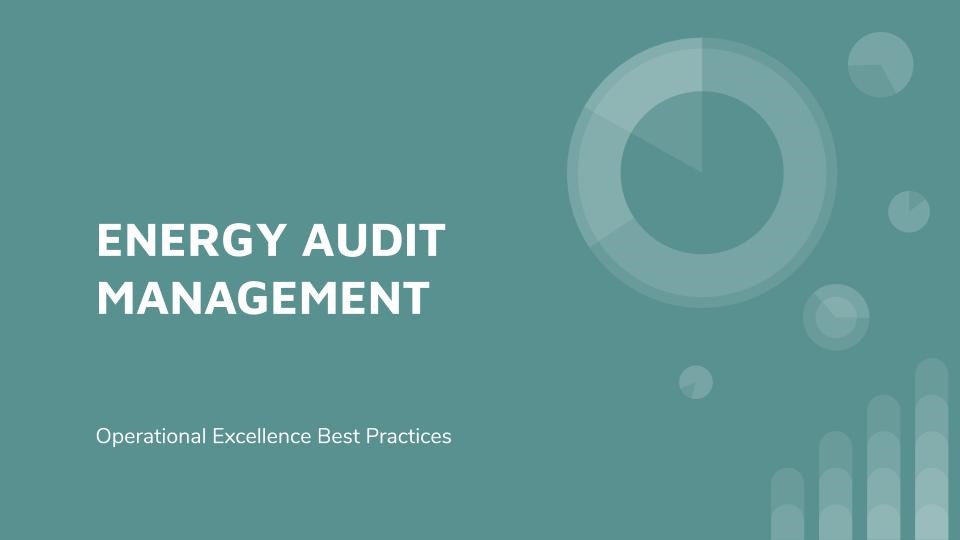
As a globe, we have learned the importance of respecting the Earth. With the advent of global warming it is now the current mandate of all industrial organizations to reduce their carbon footprints by the year 2030. As an organization, if you haven’t already started working on your carbon impact, it will be in your best operational interest to ensure that you are aligned with the global desire to restore the health of the Earth. One of the critical parameters that we can look at in order to accomplish these objectives is the advent of the Energy Audit.
At this point in time, the majority of the globe is reliant on fossil fuel in order to sustain operations. As technology advances, it is now possible for organizations to actually achieve their goals via the utilization of renewable technology, or even via the optimization of the fossil based fuels that are currently being consumed. How then can these objectives be achieved? As with all Operational projects, one can approach all projects with an A3 approach. As an organization you can look at your: Background, Current Condition, Target Condition and create an Action Plan.
The process of developing an understanding of your current operational performance and its impact on the carbon economy is known as an Energy Audit. Working with the Problem Solving methodology, there are a series of actions that one can take in order to achieve a desired operational Energy performance.
Generating the Energy Performance Background
As an organization, the first step to understanding Energy performance is to thoroughly understand how much energy the organization is utilizing for its current operational performance. A checklist that the organization can utilize is outlined below:
- Historical Energy Usage: You will need to conduct this in detail as far as the data will allow you. The more data the better, so that you can actually predict any trends that will identify if there have existed in your operational performance any peaks and troughs. Where possible, identify what caused the changes. Did you increase production? Was a critical unit out of operation, causing a reduction in performance? Note all these things.
- Understand your energy contracts. As an industrial plant how much energy do you generate yourself? At what cost? Are you purchasing your fuel and at what cost? Are you generating your power and at what cost? Do you import any deficits and at what costs?
- What are your consumption levels like? How variable is your operation? Are you continuous or batch operated? For a continuous process what keeps you at peak production and what affects your operations? Can you achieve the same level of production with less fuel consumption?
- Is the site fitted with automatic sensors for light management?
- Are all light bulbs in a current technology such as LED lighting?
- How are office spaces managed? Hows are air conditioning units managed?
- How is the plant configured? Are all pieces of equipment operating at peak? Can any changes be made to the configuration to optimize energy usage? Can any units be removed to cut back on energy consumption?
- How efficient is your compressed air system? Air is the most expensive utility. It is generated via electricity. How efficient are your compressors and dryers?
Current Condition
From the data generated above, you can then determine how the plant is currently operating. Categorize the major silos of energy consumption. These can include:
Steam Generation
Power Generation
Air Generation
Utility Consumption Profile
Knowing how all of these critical parameters can then allow you to create profiles of the plant, and to create opportunities to then start optimizing the plant consumption.
Target Condition and Action Plan
Knowing how your plant performs will then allow you to determine how best to move the facility towards the desired good. Once you know the current performance, your engineering team will then be able to identify what your target operating performance should be. From various operational sources, you can identify what benchmarks for your size plant should be. Sites such as the Energy.gov website does facilitate these types of estimates for comparative noting for your team.
If you are performing to standard, you are operating at your point of efficiency. If you still have room to grow, you can work with best practices to identify what operational practices will work best for you in order to change your energy profile. These changes can include:
Power Management Systems
Steam Management Systems
Compressed Air Management Systems
These systems are part of industrial standards, and you can always investigate how to benchmark yourself to these systems and even identify how best to achieve best practice standard. From your action plan and your actions, you’ll be able to achieve plant optimization. Where necessary, you can encourage your team to actually do things like accomplish new Energy performance records, and even offer incentives to your team.