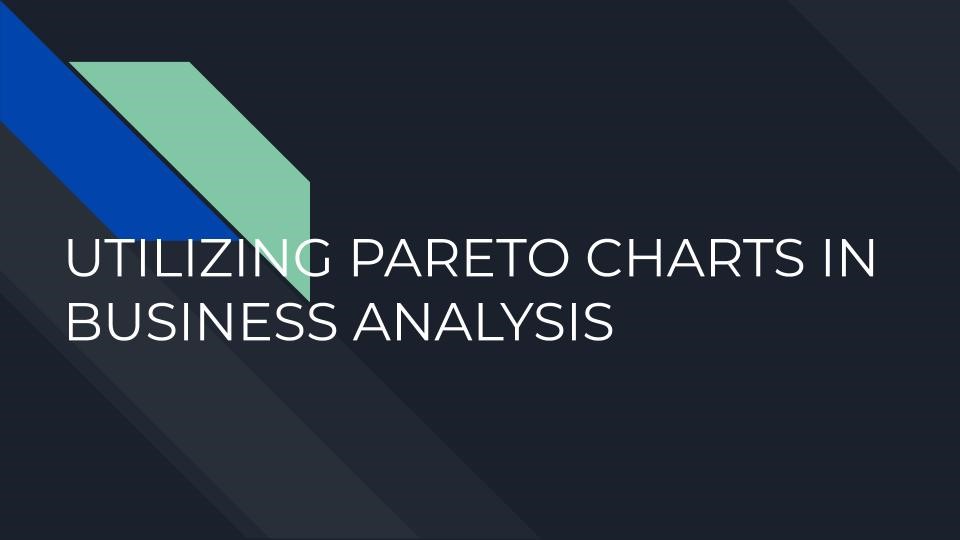
There is an adage in industrial statistics that states that what gets measured, is what will get managed by an industrial organization. If there’s anything that 2020 has taught us as a globe, it is that we need to ensure that we are more resourceful than ever. Within an industrial cycle, be it a monthly one or a weekly one, there will always be moments where individuals can identify opportunities for improvement. With the myriad of tools that are available for system assessment, it can sometimes become confusing to determine what the organization needs to prioritize in any given time frame.
The Lean Industrial Organization is ideally one that will have a built-in Daily Management system, that contains the tracking of critical process parameters across an operating platform. Within this daily management system will be critical process Key Performance Indicators or KPI’s that the industrial organization will have identified as critical to the operations of that facility. Depending on what the organization is producing, these KPI’s can include themes such as Energy, Cost and Quality.
The overarching parameter will ideally have a monthly or daily target, assuming that the industrial process is a continuous one. The levers which are then influencing that parameter can be identified and monitored in the Daily Management System. During the week, the critical operational departments can then monitor the progress of the parameters. If there were any shifts in the parameter performance, a note on the operational board should then be collated.
For auditing purposes that are both internal and external to the organization, it will be in the best interest of the organization to collate this data and identify what enablers are working as they should, and what enablers are in need of optimization. One of the auditing tools that facilitates an overarching summary of a KPI’s behaviour is known as a Pareto Chart.
Statistically, a pareto chart is represented by a bar graph. Expanding on the different axes of the Pareto chart, the bar heights will depict either the parameters of frequency or cost. These levers are the levers that best depict impact. For example, equipment uptime will be relevant to the efficiency of a system. If a system has a pump that keeps tripping or losing its packing, during a report, the engineer will then identify the frequency that the pump was out of service, and indicate that this is a critical contributor to the lack of efficiency.
Since the bars are representing impact, they levers for a parameter are arranged with the longest bars to the left of the chart, and the shortest bars to the right. With the cause and effects very clear, the department can then decide what it wants to focus on in terms of higher priority items in a system assessment.
WHEN IS THE BEST TIME TO UTILIZE A PARETO CHART IN YOUR SYSTEM ANALYSIS?
- When conducting root cause analyses and want to delve into frequency of occurrences of particular events.
- When skimming through a pool of data and want to identify the most significant factor
- For presentation purposes. They make great additions to monthly reports. Management teams are easily able to identify high priority items and make critical decisions that will impact the organizations system performance.
PREPARATION OF A PARETO CHART
For an industrial process, usually engineering teams will prepare monthly reports identifying how systems performed with time. Process and reliability engineers usually understand the day to day operations of their process systems. They will work with the operations teams to ensure that the units are functioning as they should. At the end of each production cycle, typically a month, the engineers will identify if the system performance is up to par. If there were any discrepancies, the pareto chart will be the ideal depiction of what went wrong, and how many times it did. This is how an engineer will prepare the pareto chart.
Step #1: The engineer will identify what parameters will be critical to the operating unit. This can include items like system temperatures, pressures and flows.
Step #2: For the pareto chart, identify what measurement unit will represent the unit best. Are you tracking savings? In that case you’d focus on cost on the y axis of the bar graph. Are you tracking occurrences? Then utilize frequency. This is handy for tracking activities like heater cleanings. For inventory, you’d focus on quantity. Time is the other parameter that is utilized. If you were tracking performance or tracking how long employees take to do a specific task, you’d then focus on the time parameter.
Step #3: For a particular chosen time frame, typically one month, system engineers will then collect the relevant system data and collate it to reflect the critical parameters that influence the KPI, as well as their frequency. Dissect the operating unit into critical parameters and utilize those to form the frame work of the chart.
Step #4: Based on the scale chosen, you’ll then be able to generate a graph that will be indicative of the performance of each criteria to the measurement unit chosen. Place the bars with the tallest to the left, and segway till the shortest ones are to the right of the graph.
On the chart, towards the right hand side, ensure that you have the percent impact of each of the impactors to the KPI. Match this percentage scale with the frequency scale. Link the data with a cumulative scale of sorts that will enable you to see the contributions of each item.
With a myriad of focus parameters in an industrial organization, it will be critical for system engineers to ensure that they are tracking the performance of these items. Monthly audits will be an ideal way for systems engineers to understand what unit parameters are affecting performance. With each month, the system will pretty much speak to you, and you can determine what the focus areas will be for improvement in the months and weeks to come. As a tool, the Pareto chart is a great visual tool that will guide an organization towards improvement.