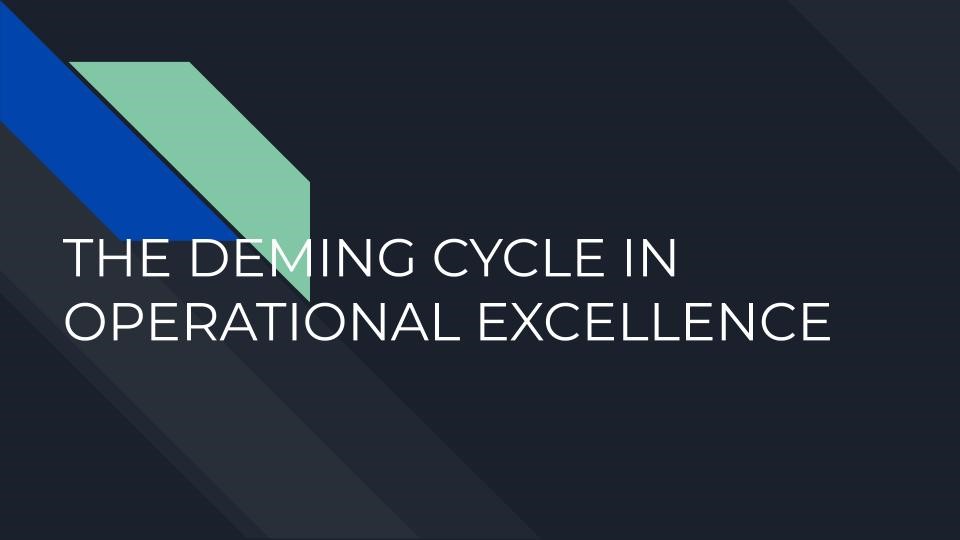
“If you can’t describe what you are doing as a process, you don’t know what you’re doing.” – Deming
Industrial Organizations can utilize technology to optimize their systems. Those that do, are often ahead of the pack. Organized as a central system, the Deming system provides the appropriate management teams with feedback on the system’s performance where resource utilization is concerned. Managers focus on various entities during the organization’s project management process, as well as during its operational runs. A Deming Cycle is one such means that facilitates this process. The various elements that are monitored a Deming system include the suppliers and the end users or customers, and the myriad of entities in between.
With an appropriate feedback loop, managers are able to identify which aspects of their operations are under, over or appropriately utilized. Competition is always a concern for any thriving organization. Competitive Advantage is a moving target, and cost optimization will always be a tool that the organization’s management can utilize in order to facilitate its core operating objectives. An appropriate investment in a Deming Cycle, will guarantee organizational success.
With a lean industrial environment, the need to ensure that an adequate feedback loop exists within an organization is key. What gets measured is what will get managed, and it will be important to have an accountability cycle that facilitates the ability for an organization to see itself and its performance. Such as a system is known as the Deming cycle. With the proliferation of Operational Excellence tools across the industrial sphere, the Deming Cycle is also now popularly known as the PDCA cycle.
As a continuous quality improvement tool, the PDCA cycle actually takes you on a journey of a sequence of steps that flow into each other. The cyclic process: Plan, Do, Check and Act is designed to keep a system in a state of continuous flow. The Deming Cycle is actually designed to be a spiral of sorts, that will enable a system to keep its focus on a particular forward goal.
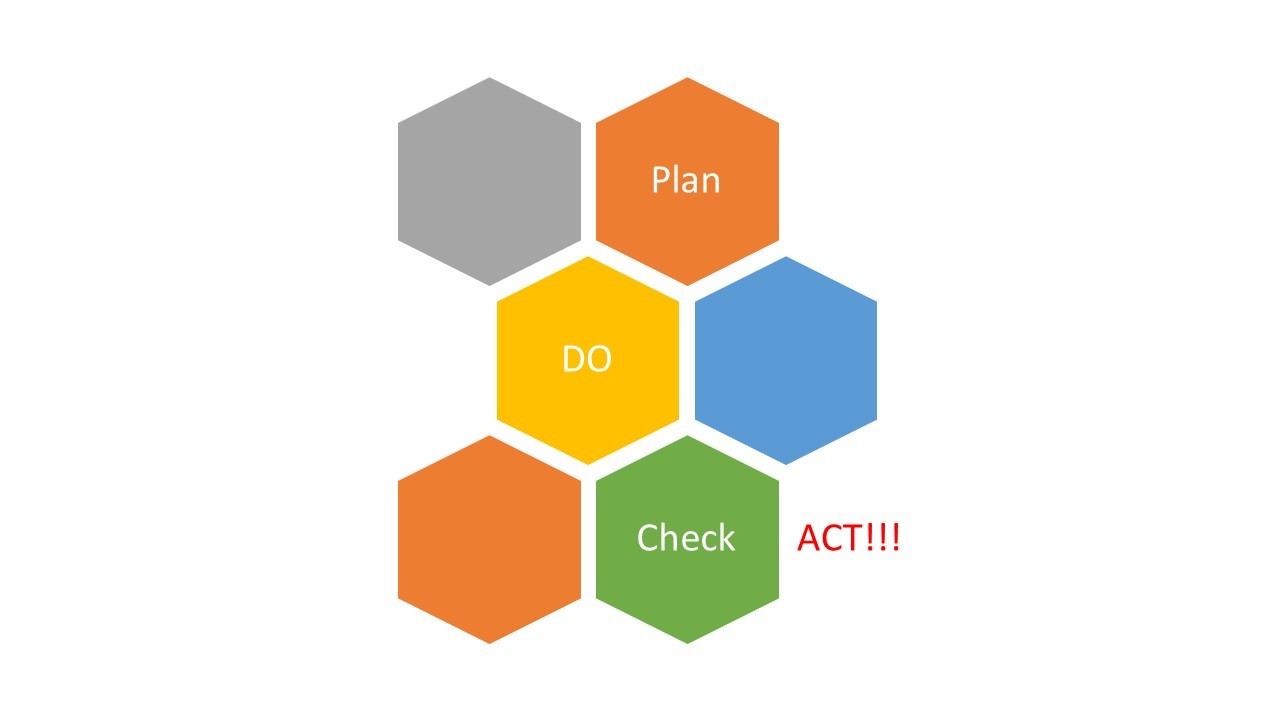
Let us now dissect the Deming Cycle and see how best we can allow ourselves to flow through this continuous improvement cycle.
PLAN: The principle of planning, is one that gives an organization a direction. The aim is to plan ahead, so that the organization can sustain itself a competitive advantage. For an industrial complex, it is always a good idea to have a predetermined forecast for the year, that will identify what the key Key Performance Indicators will be. This will determine what the critical targets will be in terms of costs for operational runs, targets for resource utilization, and where possible, an organization will do its best to exceed these targets from a cost cutting perspective.
DO: Once the plan is in full effect, the aim of every organization is to execute its plan. Ideally, from the strategic level, there will be a means that the organization can then trickle down its visions into the various departments’ operational systems. Utilizing systems such as Daily Management systems, organizations can then take the time to ensure that Key Performance Indicators are then in the eyes of the operational arms.
CHECK: With the utilization of systems such as daily management systems, organizations can then identify if they are complying with the requirements for that particular KPI. If the parameters are monitored, the departments can then build in the relevant action plans that the department can utilize in order to restore the parameter if there is a shift. If all is well, then there’s nothing to be done and the process can simply flow. If there’s a shift, the department will then proceed to the ACT section.
ACT: Defined as the continuous improvement section of the chart, this enables an organization to take action to standardize or improve the process. This can be in the form of actions such as kaizens which identify if the system is to be improved or not, or can simply involve the activity of restoring a system via systems such as problem solvings if parameters are off spec.
With a daily management system in place, organizations will be well on their way to ensuring that their targets are being met. With continuous monitoring, you are ensuring that your organization understands itself, and that any areas of weakness are easily restored.