The Taguchi Loss Function proposed by the Japanese quality expert Genichi Taguchi states that any deviation from the desired target value or specification results in a monetary loss to society. In this context, the Taguchi method is based on the hypothesis that the smaller the variation with respect to said target value (goal), the better the product quality. Note that the desired target value or specification is equidistant from the Lower Specification Limit and the Upper Specification Limit.
Taguchi’s contribution lies in incorporating the perspective of the client in the analysis, given that in general there is practically no difference between a product that is just within the limits of specification and a product that is just outside of these. On the contrary, the difference turns out to be much greater in terms of quality, when comparing a product that has the target specification (objective) in relation to a product that is near one of the specification limits.
In order to better understand Taguchi’s proposal, it is convenient to contrast his vision in relation to the Traditional Perspective. According to the traditional concept, losses occur only when a product exceeds the specification limits as shown in the graph. In this way it is assumed that any product that is contained within the specification limits does not generate a loss in terms of quality for the customer and for society.
This approach is simplifying and, in some cases, could be found reasonable, at present there is a consensus that it is considered obsolete, as it does not adequately represent the client’s assessment.
On the contrary, the Taguchi Loss Function establishes that there is a degradation of the quality from the perspective of the client when the product moves away from the desired specification even when it is between the specification limits.
Stages of the Taguchi methodology
- System design: This is the conceptual stage in which the general characteristics, parameters to be taken into account, objectives, etc. are determined.
- Design of parameters: Once the concept is established, the detailed engineering stage begins, in which the parameters of the product are defined: dimensions, specifications, materials, etc. In this stage an analysis allows to establish parameters that minimize the effects of the variability in the process, environment and manipulation in the final performance of the product. In this stage, a series of statistical experiments can be carried out that help to measure the sensitivity of the objective parameters to variations in the process or in what are called noises.
- Design of tolerances: Completed the design of parameters, and with a real understanding of the effects of each of the parameters in the final performance of the product. You can focus attention on a few key parameters, which will work to obtain closer tolerances.
The Taguchi method is based on two concepts with a focus on improving the quality of both the product and the process, these are:
- Robust quality: Consistency of quality.
- Quality loss function.
Robust Quality
The concept of robust quality has a product-oriented approach, that is to say that units that can be produced in a uniform (consistent) manner should be designed, despite processing in an adverse environment. The priority in the Taguchi method is not the adverse manufacturing conditions, which can be considered as causes, but the design of the product, so that an adverse environment has no effect on the quality of the units.
The premise of this approach is to avoid that variations in the quality of the manufacturing environment, which can be multiple, affect the quality of the product.
Quality Loss Function (QLF)
The function of loss of quality, widely known as QLF by its acronym in English Quality Loss Function, establishes the behavior of the costs associated with the deviations of quality with respect to the goal. So that the product, in terms of quality, ceases to be simply cataloged as compliant or non-conforming, to be measured by a function that establishes the cost of moving away from the exact specifications of the client.
Taguchi defines the quality as follows:
“Quality consists in avoiding a loss that a product causes to the company, after having been shipped, different from any other loss caused by its intrinsic functions”
In that order of ideas, the cost of moving away from the exact specifications of the client may include the following items:
- Maintenance Costs.
- Repair Costs.
- Costs associated with operating failure.
- Costs associated with injuries caused by a defective product.
- Logistical Costs.
- According to the Taguchi hypothesis, the smaller the variation in relation to the target value, the better the quality; The losses increase at an increasing rate as the deviation from the target value of the specification grows.
Likewise, there is a loss of quality from the customer’s point of view when the product moves away from the desired specification, even when it is within specification limits, which contrasts with traditional variation control methods.
It can be seen that the function of the loss of quality is a U-shaped curve, which is determined by the following simple quadratic function:

-
- L(x)= Quality loss function.
- x = Value of the quality characteristic (observed).
- N = Nominal value of the quality characteristic (Target value – target).
- k = Proportionality constant.
Proportionality is a factor that indicates the constant relationship between the cost of loss and deviation magnitudes of the quality characteristic. Thus, for application purposes, it is necessary for the organization to record the losses according to the cost of the quality of the units according to their deviation from the target value.
So then, the function can be expressed as follows:
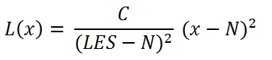
-
- C = Cost of the deviation in the limit of the specification (Loss for a unit produced in the specification limit).
- LES = Upper specification limit.
- L(x)= Quality loss function.
- x = Value of the quality characteristic (observed).
- N = Nominal value of the quality characteristic (Target value – target).
- k = Proportionality constant
To conclude, remember that although the QLF quality loss function hypothesis is far from the traditional variation control methods, it does not mean that they are opposed in practice. In fact, it is common for many companies to choose to implement a variation control model based on conformance with respect to specification limits; and then, implement the function of loss of quality as a philosophy of continuous improvement, with the purpose of focusing on the perfect product for the client.