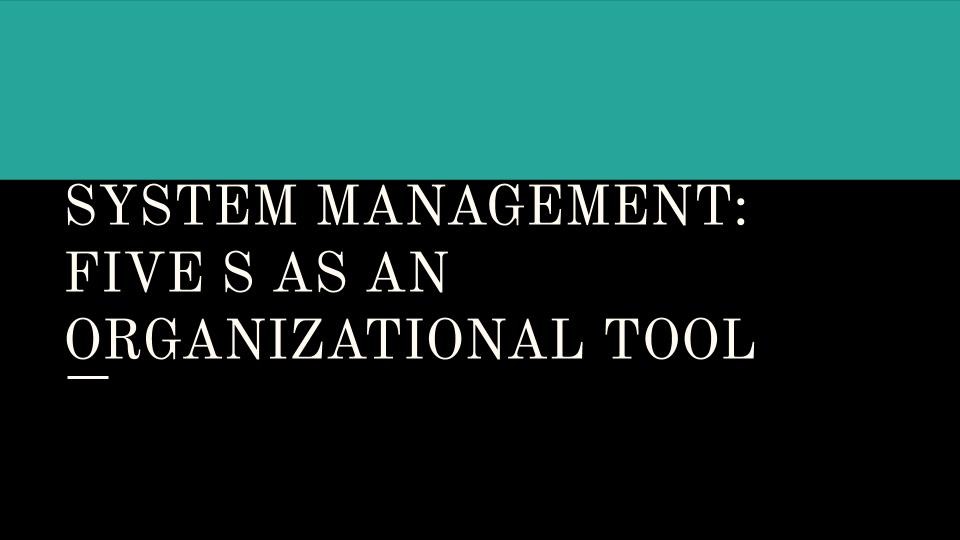
The Universe is one that is composed of order and patterns. Our lives are such that we thrive off patterns. Knowing what will happen, when it will happen, where it will happen, will ensure some semblance of stability and order in an organization. 5S in the industrial sphere, is another process tool that will ensure that there is calm where there previously was disorder. There is just something about having a clean space, that makes it feel like an environment where people will want to work in a manner that is safe and efficient.
If you thought you were efficient and organized, 5S is that industrial tool that will take your level of organization to the next level. We are all about levelling industrially in 2020. Industry 4.0 tools, Lean Tools, Six Sigma, Operational Excellence and TPM are all tools that will enable your organization to achieve its peak performance. Ideally, you want to know where everything is and once you do, you’ll allow yourself to be in a position where you can coordinate your staff to actually enable the relevant work to be achieved.
5S Origins
Originating from Japan, the 5S methodology is based on five main ideas: Seiri, Seiton, Seiso, Seiketsu, Shitsuke. For those of us who thrive in the West, the English translations are: Sort, Set in Order, Shine, Standardize and Sustain. As simple as these tenets are, they are still relevant in 2020! A spotless plant is a productive plant. It means that the staff is on top of their activities, all housekeeping is in order, and that the autonomous maintenance and relevant equipment related attention is being achieved. You want your organizational staff to be in tune with their surroundings and with their equipment. Knowing where everything is, is the key to ensuring the longevity of the facility. From the mid-20th century to the new millennium, we still welcome the relevance of 5S. Good, clean results have been proven to come from a clean, organized plant.
Competitive advantage is a moving target. As a result, it always helps to ensure that the organization understands the benefits of a tool before they use it. Cleaner spaces cost less to maintain. Production quality will be maintained because the equipment will be operating as it should. Greater employee morale will come from the fact that the employees will love the environment where they will be living and working for the next few years. Shiny paint works wonders for employee morale. If the plant feels like a home, the staff will actually want to stay there longer and deliver satisfactory results.
5S IN AN INDUSTRY 4.0 WORLD
Sort
With industry 4.0, the movement towards automation is one that many organizations will have to ensure is facilitated. The team will have to go through all their equipment, and determine what will be kept and what will be discarded. Sensors and such equipment require the utilization of process wires, so organizations will have to ensure that when these items are installed, the wires are neatly tucked away from the body of the machinery and from the main shop floor. If there is any equipment that is not needed in a space, it can be repurposed or sent to storage. Tag the items from an organizational perspective, to ensure that the items are recognizable.
Set in Order
Decluttering allows you to see what items you will utilize. Group the necessary items, and identify where they would be most suitable for housing. Where necessary, ask your facility to ensure that there’s a shelving unit that will provide you with the space to hold your tools.
Shine
Having a routine for the operational staff that ensures that the staff is cleaning up the work area is an idea that is important to an organization. With a means to ensure that the equipment is clean, you will serve the dual purpose of ensuring that the plant itself is operating at peak. During cleaning, the staff can identify if everything is in order.
Standardize
Another Operational favorite word, standardizing is the key to ensuring that items are organized in a systematic way. Everyone who is performing the task and organizing the equipment after the system is organized will be able to organize the items as their predecessor. What helps is the use of a shadow board, with the outline of the items, or a label indicating where that item should go.
With time, there will be the ability to ensure that the industrial space is kept in order. With the ability to clearly see what the organization is working with, they will have the ability to keep their operations seamless.