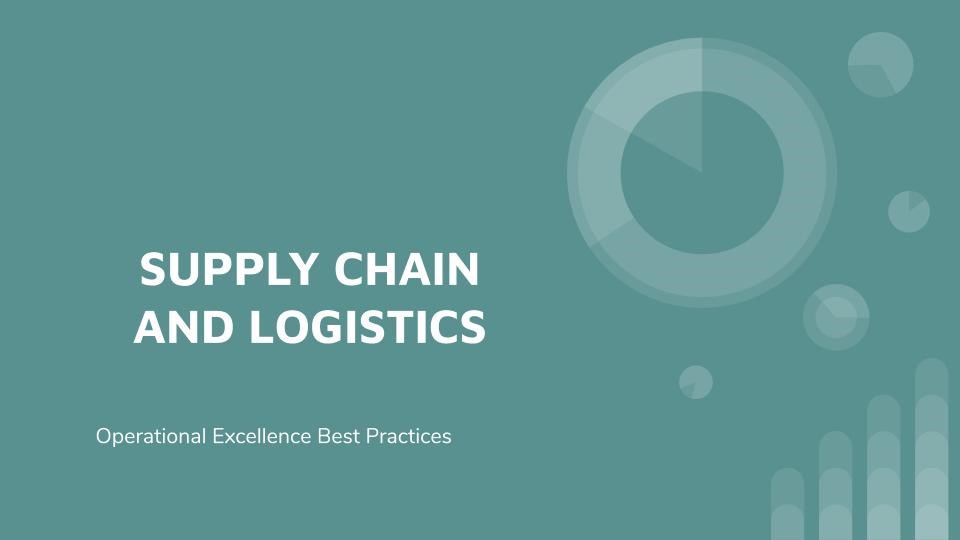
In an operational flow, there is always a flow from the supplier to the customer. Large operations have to place themselves in a position where they are able to master their supply chain, just to ensure that they are in an agile operational flow. Inventory is very pricey, and it will be important for organizations to understand how to manage this one lever, in order to ensure that they are able to keep their costs at a manageable status. One critical thing to master from the operational perspective, just to ensure that the supply chain is responsive to the needs of the customer.
When you look at an industrial plant, you are actually looking at a logistical and operational masterpiece. With various elements at play, it is always a great idea to ensure that the flow of inventory from the initial raw material warehouse, to even the customer via a delivery outlet is clear and accessible. Where large volumes of product are involved, it will be important for an organization to ensure that it has an effective and efficient pipeline. From a production perspective, commit the organization to a just in time system that will facilitate the enabling of cost optimization and resource management improvements.
Industrial plants are part of a large global retail supply chain, and the parameters that operational managers in these entities tend to focus on include parameters like inventory turnover as a lever that influences the operating profit. The stock history of an organization will indicate how effective an organization is on the retail market. As an organization grows, with a large output being generated, it will always be a critical focus of the company to ensure that it is able to successfully manage its flows to sustain the business.
Large global operational chains like Walmart have managed their supply chain in order to optimize product distribution. We will utilize them as a best case scenario for the conditions where we as a manufacturing entity are producing products that we will then need to ensure are reaching our end customer. Inventory starts in the warehouse, but we really don’t want it to stay there forever. It will have to be transported to the final customer in order to ensure that the business relationship will grow and expand.
Walmart’s vision as a global supplier is to provide their customers with the number of goods that they want in the time frame that they want them in. Fusing in their cost structures that facilitate the product pricing, the company was able to accomplish their objectives. By concentrating on a structure that is highly organized and advanced, the company was then able to generate market leadership. From an Operational Best Practice perspective, they are a benchmark worth studying and learning from.
Supply Chain innovation in the company started with the simplification of the supply chain. As a product driven organization, Walmart started their process of bulk merchandise purchase, subsequent to which they’d actually transport the product directly to their stores. This was the initial phase of optimizing their supply chain. The next step involved ensuring that the company had a direct relationship with their manufacturers in order to negotiate the best operational costs. Industrial plants can benefit from this tactic by ensuring that they are able to remain in close contact with their upstream manufacturers or suppliers to ensure good and suitable pricing mechanisms.
Open Systems
Walmart as a large organization has a supply chain initiative called the Vendor Managed Inventory system. This system involves ensuring that manufacturers are responsible for their products in Walmart’s warehouses. In some instances, you may have suppliers of critical supplies such as flocculants on site, oil treatments or even boiler water treatments. The more care that the supplier has for the product, as well as their awareness of the products in your own inventory systems will ensure that the relationship between the two of you is maintained.
With a strategic vendor partnership, the company will always be poised to access the best price from the suppliers. With long terms and high volume purchases from your suppliers, you will generate long term relationships. Collaboration is the king of supply chain success.
Re-stocking
Walmart’s inventory tactics have helped to optimize their inventory efficiency. Utilizing a just in time system that facilitated direct product transfer of products, has made them very successful indeed. The organization transfers products from inbound trucks directly to an unload on an outgoing trailer or rail car. There is no storage in between the transfers, cutting down on the inventory storage costs associated with intermediary warehouses. This strategy is known as cross docking. While in manufacturing, there will be an ideal buffer zone, bearing in mind that there is no perfection in operational flow, it will always be helpful to ensure that as best as possible, you are operating in a zone that is from the plant to the truck or to the ship.
Maintain a good supply chain flow and you’ll be well on your way to good Operational success. Walmart as a benchmark, has managed their supply chain so much that their costs are up to half the costs of other comparable retailers. It is always good to monitor the best, and see how best your systems can match theirs.