Compared to DMAIC’s define phase, which deals more with identifying the problem statement, the measure phase engages more on collating data and making extensive analysis, numerical and statistical studies. The focal point of this phase is to identify which metric gives the highest effect on the problem. Those who give greatest impact are prioritized to create a list that will be studied in detail. With a prioritized list of data in hand, the project owner will then determine the probable ways the procedure could go wrong or how the data may perhaps go wrong. Legitimate and dependable metrics to observe the progress of the assignment are established during this phase. Once the grounds for data failure are identified, anticipatory action items will be created.
The objective of this phase is to determine the significant measures that are essential to assess the success, meeting significant buyer requirements and start developing a procedure to effectively gather data to quantify course performance.
There are several quantifiable tools used during this phase. Just to name a few: Process Mapping, Data Collection Plan, Leading and Lagging Metrics, Descriptive Statistics, Histogram, Capability Analysis, Sample Size Collection. Some project owner use more than one tool before drawing a conclusion.
A process map is a graphical demonstration showing the stream of work through the course in changeable degrees of factor. This is best illustrated as the relationship between X and Y. X representing the input and Y representing the output. This is mainly used in gathering the voice of the customer or VOC to determine the overall course outputs and production requirements of the clients. The benefit of using this tool is that this provides the foundation for making work directives and/or job aids.
Process mapping can be done using SIPOC, High-Level Process Map, and Detailed Process Map. SIPOC sets the range of procedure to be analyzed and arrests the voice of the customer or the production requirement. High-level process map on the other hand, defines the foremost steps or the sub-processes of the one after the other procedure. This classifies the X’s and the Y’s for every process step, identifying them whether they are uncontrollable or controllable. This is where the primary identification of significant process inputs is done. Detailed process map describes the step-by-step stream and conclusion within a course. This also provides foundation for representative training and orientation.
Measure it the Six Sigma Way
A diagram below shows the start-to-finish call flow of a technical support agent. Each stage is characterized with several activities that might lead to customer dissatisfaction. The middle row boxes represent the first-to-last stage of the call. The first row boxes represent the outputs and the last row of boxes represents the inputs.
Inputs will be classified whether it is controllable or not. Inputs can also be classified as critical or similar to critical to quality (CTQ). Critical inputs are assumed to have foremost effect on the procedure outputs.
Every stage in the process should be carefully evaluated based on the significance it provides to the customer. There are three classifications which identifies value of a certain process. These are:
- Value Adding, this is where important stages are to transmit service according to the customer’s requirements. To identify if a process is value adding, the process should be completed correctly right at the fist time, customer doesn’t have any complaint about it and very much willing to pay for the final product or service.
- Value Enabling, this is where some stages are not value adding for the clients but gives overall greater efficiency or effectiveness in the process.
- Non-Value Adding, this is where stages do not qualify for either value adding or value enabling. Most of the activities included in this stage needs improvement.
Another tool used in measure phase is the Metrics. This is where leading and lagging metrics are identified. This process uses metrics to guide course management and course development activities. The advantage of using this tool is that this enables a wide-ranging understanding of course performance. This tool provides the project owners to effectively handle service delivery functions through better decision making. This tool also allows detection and prioritization of course development opportunities:
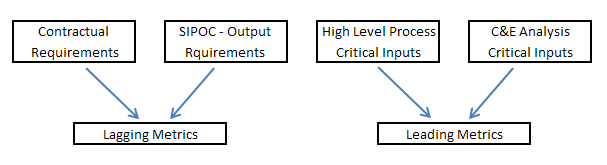
To identify leading metrics, record all inputs from the high-level process map. Determine the significant inputs using the Cause and Effect table. Record all significant inputs on a transfer function template. The final list will be the leading metrics.
The Cause and Effect tool is used in determining the critical course inputs that have the greatest impact or effect on the overall course performance. Since the table comes with weights that help calculate the inputs, it is then easier to identify which amongst all inputs gives greater impact on the course. All inputs indicated in the high level process map should be included in the cause and effect table. In the same manner that all output requirement in the SIPOC table should be included in the Cause and Effect table:
Weights assigned on each output will depend on how significant the output is. Using the given weights, the project owners will assign weights on each input relevant to a specific output. This will then be multiplied to the assigned weight of each output. All products on each input will then be added. Based on the diagram above Step 2 is more critical than Step 1. Step 2 will then be prioritized when making action items.
There are several other tools to measure data. In scenarios where there a voluminous sets of data sampling can be done. Instead of getting the entire set of data, project owners can just get a sufficient amount of a data.
Histogram is also used to help assess the shape, spread, and center of data set. This is best used when there are at least twenty-five sets of observations. The whole range of information is divided into a number of period of identical size also called intervals, cells, bins, or classes. The bars of the histogram will display the number of observations falling into each period.
Use of several tools only drives the project owners to one thing – that is to make a sound analysis that will eventually give an effective action plan.