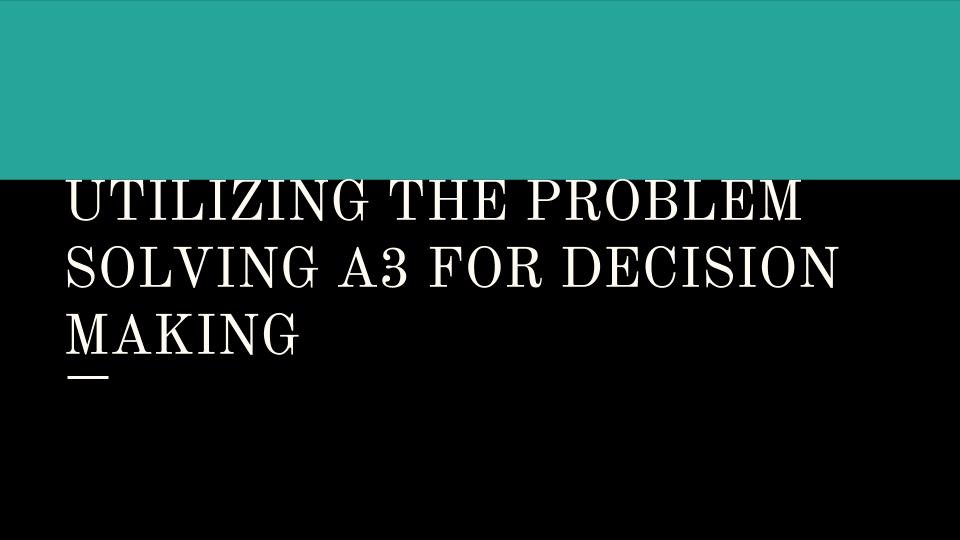
Industrial organizations thrive on order and structure. Once a customer’s order is placed, Operations Managers love to know that everything will flow seamlessly from raw materials to customer delivery. Of course…life in idealism is different from what life is in reality. In the real world…the industrial process is smooth on most days. You do have the occasional day when a boiler will trip, a tank will overflow because the level controller reached its lifespan, or a pump will lose its packing and leak.
This is the reality of industry. The beauty of industry however, is that it’s a self learning mechanism. With the persons who work inside the facility studying it, a plant can self heal and it can restore itself to having either minimal downtime for maintenance or relatively few occurrences of equipment malfunction. The key to ensuring that a plant is at peak, is the problem solving exercise.
This activity is one that is embedded into daily management systems as part of the means that the organization will take to counter parameters that have been out of target for a count usually of three sequential days or in some instances shifts. Process parameters staying on target will be key to industrial performance, and it is in the best interest of an organization to ensure that there are reaction plans in place that will restore target conditions once there’s a shift. While parameter targets are not set in stone, for most processes, there is a desired range that must be upheld for the sake of quality management. Out of specification products are expensive and it is important for an organization to ensure that it is staying within parameter targets to avoid these costs.
THE PROBLEM SOLVING EXERCISE
Anticipating that there is a problem on the plant, the department superintendent or the department’s operations engineer will take the time to actually ensure that the relevant parties in the department are investigating the root cause of these issues. The persons on a problem solving team often include the process engineer, the reliability engineers (mechanical and electrical) and also the operations staff who observed the phenomenon.
In the problem solving meeting, there are actually several tools that the team can use to achieve the objective of identifying the root cause of a problem. Documenting the process however, is best done on a document known as a problem solving A3.
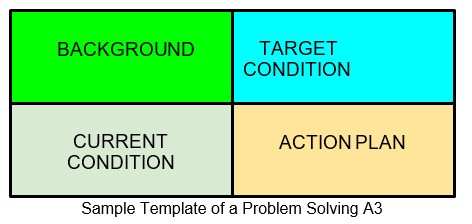
The problem solving A3 is an ideal way that the process of identifying the root cause of a system can be identified and documented. In some instances, industrial problems do recurr, and having a detailed thought process on file, will enable the team to look at previous work that was done and enable the solution to be quickly found.
Section Analysis of the A3 Document
Background: As a team, put on your scientific thinking caps and start identifying the background of the current condition. Utilize a description process like the 5 W’s as a means to create a background baseline. What, Where, Who etc, was involved in the process when the discrepancy was detected? Where necessary, pull some data, print a graph and attach it to your file. If you wish, you can calculate relevant savings.
Current Condition: The current condition is an indicator of the system’s performance now that the shift has occurred. You can look at it in a myriad of ways. For example, if a tank overflowed, the current condition would include a description of a decreased process flow into the tank, or an increased flow out of the tank. This section will include the adjustments made due to the initial shift. It is not a description of the solution, it will be a description of a countermeasure for the most part. This will be because the root cause will not automatically be known at the onset, but operators are taught to have a baseline reaction to rectify and they usually do.
In this box, you can take your time and build out your fishbone diagram and discuss the root cause of the problem. You can either do the diagram on the front of the page, or turn the paper over and do the fishbone diagram on the back of the page.
Target Condition: The target condition is the desired set point that the system needs to achieve. With the fishbone diagram completed, the team must by that stage have a good feel for what the target condition should be. The system targets are pretty much preset, so you can start with them there. If desired, you can also take the time to revise the target condition.
Action Plan: The action plan is an itemized list of actions to achieve the objective, as well as the responsible person for this task. What is key is a due date, so that the actions and their completions can be tracked. One key person, such as the process engineer, will ensure that the department is executing the desired targets, so that they can then be completed, and the system returns to normal.
A3 Thinking is a good system that an industrial plant can utilize to ensure that it is meeting organization operational parameters. When there’s a discrepancy, the team can either refer to previous problem solvings, or if the problem is new a fresh document can be generated to facilitate a new root cause.