In the previous article, we commented about the basics of Lean-Sigma methodology and its relationship with the experimental scientific method, such as concepts for optimization of pharmaceutical manufacturing processes.
Today, we will discuss about a case study of optimization of a pharmaceutical manufacturing process using DMAIC.
Today’s case study consisted of optimization of a wet granulation line. Following flow chart outlines a typical manufacturing process of pharmaceutical tablets. Red blocks are part of the process that we will focus in this case study.
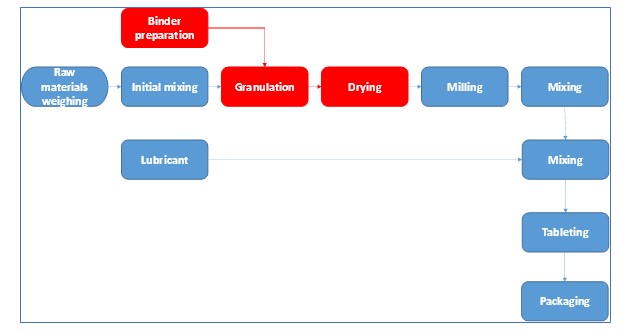
Following, case study in the DMAIC sequence will be presented.
This blog is presenting in detail the case study only up to the stage that demonstrates that it is feasible to change the process and getting a product with acceptable quality characteristics.
Increasing installed capacity of a wet granulation line in pharmaceutical manufacturing
1. Define
a) Identify the problem
There is a wet granulation line occupied at 130% of its capacity. It consists of a high shear granulator and a fluid bed dryer. Now, a second fluid bed granulation line will be installed at the facility.
b) Setting the target
Demonstrate that it is feasible to balance the installed capacity of both of the wet granulation lines, transferring some of the high shear technology products to the fluid-bed granulation technology.
2. Measure
a) Validate the problem
Information obtained from industrial engineering corroborate the information at section 1.a.
b) Measure the current process
Information obtained from industrial engineering corroborate the information in the section 1.a.
c) Redefining the goal
Data provided by engineering analysis to define the following:
• Fluid transfer products represents a release of 30.5% of the current area.
• The occupation of products to the fluid granulation line represents 35% of installed capacity.
Therefore, the objective is defined as follows:
Demonstrate that it is feasible releasing up to 64% of the capacity of the current wet granulation line transferring products to the new line of fluid bed granulation.
3. Analyze
Change from high-shear to fluid bed wet granulation process doesn’t impact negatively on the quality specification of products.
Change in the manufacturing process simplifies unit operations as well as in process control.
Number of people in the current granulation line can be optimized, from two people to a single person, since the fluid bed granulation equipment is an equipment that performs two processes —a single pot.
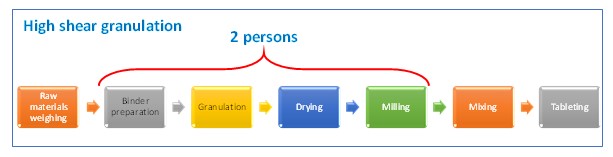
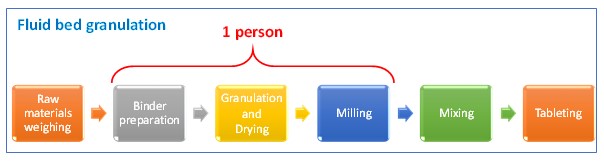
Following table shows a comparison between the current process and the proposed new one. Wastes at current process are identified and it is showed that they disappear at the proposed.
4. Improve
Working plan for this stage consisted of the following:
- Defining main impact factors affecting fluidized bed granulation.
- Defining the most significant response variables to assess the process.
- Establishing a design of experiments (DoE) according to the factors and responses defined.
- Manufacturing of pilot-scale trial batches.
- Results analysis.
- Concluding about feasibility of switching granulation technology from high shear to fluid bed.
- Performing scale-up to manufacturing equipment.
Aim of manufacturing of trial batches was to determine if there were optimum process conditions to obtain the particle size appropriate and consistent in each production cycle (batch-to-batch manufacturing). Three critical process factors were identified. A factorial DoE at two levels (23), which is presented in the following table with encoded values was used to establish optimal conditions.
Response variables selected were Cp of weight variation as well as resistance, and their respective RSD (%). Following table shows results. Most successful run was defined as the one that allowed obtaining the maximum Cp weight and minimum possible weight variation, which was achieved in the run 4. Cp resistance is less relevant, since the limits used are experimental and can be set new ones based on the statistical behavior of weight variation. Information marked with “L” were trials that showed poor resistance and therefore were not successful for the evaluation.
After this DoE an optimization one was not performed as a second step, since pilot scale was used. Final optimization DoE was done at next stage (scale-up), a surface response was used.
According to these results, it is concluded that it is feasible to technically perform the change of granulation technology.
Following stages of DMAIC, considering results obtained, but are not discussed in detail at this time because we would use more time than allowed, is performing process scale-up, i.e., manufacturing batches at industrial size and optimizing process conditions of processes through a DoE (23) factorial, two levels and evaluate with response surface to establish design space and optimal process conditions.
5. Control
Last stage of DMAIC is assuring that implementation is successful and batch-to-batch can be obtained. Current accepted criteria by drugs regulatory agencies is process validation.
Once this evidence is generated, new process is accepted to run on a routinely basis.
Final comments
For new products, ICH’s Q8 and Q9 guidelines allow products to “be born” with an appropriate robustness in such a way we can perform further optimizations within a design space.
For products that do not have a space design, Lean Sigma tools allow us optimizing processes in a systematic way at the same time we create needed documentation to support improvements according to current guidelines and pharmaceutical regulations.