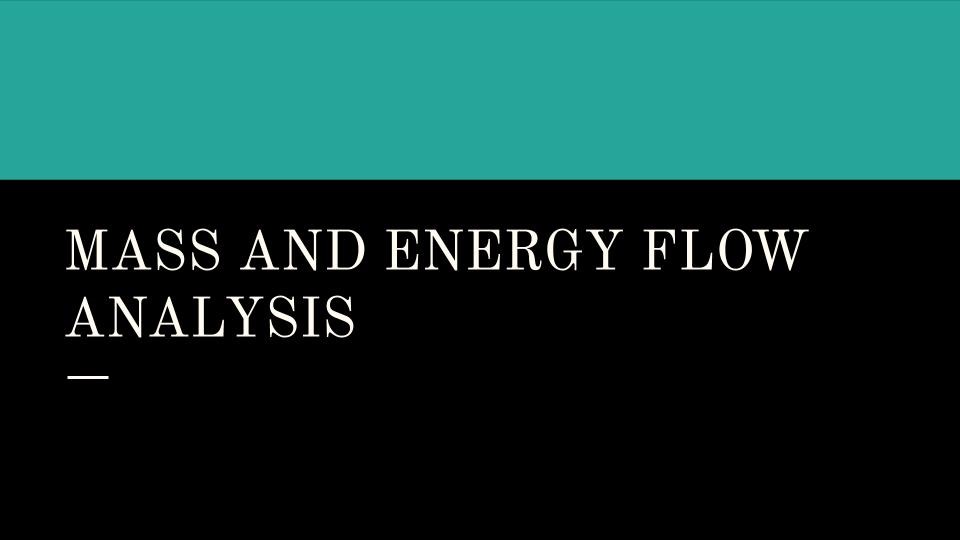
In the industrial realm, competitive advantage is a moving target. With the current global condition as it is, influenced by disruptions of supply chain flows due to the Coronavirus, it will be important for organizations to ensure that they are operating at their peak in terms of resource management. Business must take place despite the current global scenario. Organizational adaptation to the changes must take place. In the business realm, it is business as usual, but with a much slower pace than we have anticipated.
Industrial organizations can start the process of ensuring that they are in good communication with their customers. In Lean and Six Sigma, the voice of the customer is always an important factor for organizations to consider. Knowing that the global demand for products and services have shifted, it will be important for you to identify what your supply schedule will be. As a start, talk to your customer.
Voice of The Customer Meeting
If you haven’t already done so, set a meeting with your customer. This can be done either in person or via utilizing a virtual meeting with services such as Zoom or Skype. In this meeting, you can then start the process of identifying what the customer will need from you as a supplier. Is it that the demand has halved and that you’ll need to deliver every fortnight instead of every week? Is it that the quantity of critical items needed has shifted, and that you need an increase in a particular product due to the current economic condition. Is it that the formulation of a product has shifted to ensure that increases in health standards are being met? Knowing what the customer will need, will ensure that you are as a manufacturer going through the process of meeting the critical quality and quantity needs.
Just In Time Manufacturing
2020 as a year, will be the year that Just In Time manufacturing will make a peak in demand. That being the case, as an organization, you must prepare yourself to ensure that you are able to have your warehouse stocked in order to meet the demands of your customers. In a time where your demand fluctuates, warehouse inventory is something that you as an organization will have to keep to a minimum. Based on the voice of the customer discussions that you just had, you should be able to predict your anticipated production schedule, and adjust your schedule to meet these demands.
Mass and Energy Flow Analysis
Now more than ever, resource management will be critical to your organization’s profitability. If you haven’t already done so, ensure that your process engineers have done a thorough mass and energy flow analysis in your organization. If you don’t do monthly inventories, now is a good time to start. What monthly inventories will enable you to do…is identify your organization’s real needs. You’ll know if you ordered too much of your catalyst, or if you can actually scale back on ordering until the next two months and save the organization some money.
The mass and energy flow analysis will also let you know what equipment is operating at peak, or what equipment can actually be taken out of service for the interim. With reduced uptime, now is the perfect time to have organizational Kaizens, and ensure that your organization is operating at peak. With a reduced flow, you will have time to fix things in your organization. There are some critical pieces of machinery that are usually needed at peak performance, but then if your organizational output has shifted, you can take those pieces of equipment out of service and maintain them now that you have the ability to toggle your machinery. The peak will resume, it’s just that in the current condition the best that you can do is ensure that you are ready for it. Maintenance staff are often stressed during peak, so now that demand is on the lower side, they can actually take the time to fully maintain the equipment to the manufacturer’s specifications.
Production infrastructure often goes neglected during instances where individuals are focusing on production. Now’s a good time to do a little plant upkeep, paint the relevant areas of the plant that didn’t have an opportunity to be maintained.
If you have equipment that you haven’t optimized yet, now’s a good time to identify how you can utilize them via a debottlenecking exercise. Have your process engineering team run some simulations and identify if there are pieces of equipment that you can utilize elsewhere in the production site. Is it that you can have two lines running simultaneously? If so, now’s the time to have the maintenance staff reorganize the equipment and create the two lines. Where possible, you can even go through the process of tweaking operational parameters. Start toggling with different process parameters and see how best the process adjusts to these conditions.
Summary
With more time to process things, organizations can take the time to talk to their customer base, and identify the critical areas of focus in terms of production. If you don’t have a Just In Time System, then create one now or optimize your system to be Just In Time like. Has the customer rearranged their demand schedule and how will this help you as an organization? Can you tackle much needed maintenance activities? With a few kaizens, you can put yourself in a position where you will have a detailed mass and energy flow analysis done, that will enable peak performance to be achieved.