A process is composed of a set of interrelated activities within a company with the objective of providing products or services to its customers. The effective management of the processes for the production of goods and services in less time and with lower costs is a mandatory practice to ensure the competitiveness and profitability of the organization. But managing processes is a complex task, mainly because these processes do not work alone, they interrelate with other processes throughout the company.
This is why the improvement of processes has an important role in the organizations since this depends on the growth and improvement of the company with respect to the quality of its products, processes, personnel and in general, it has an impact on the recognition and competitiveness of the company.
The Model for Parametric Analysis and Organizational Evaluation, better known as Mapping, consists of a platform of tools to analyze the profile of composition and articulation of the structure and internal processes of the organizational entities, based on a frame of reference of descriptive parameters, their representation and assessment through formats of tabular and matrix type.
The purpose of the Mapping is to identify the parameters with which the internal structure and processes profile should be formulated, so that an organizational entity has success in meeting its projected objectives, goals and utility expectations, as well as in the coverage of its functions and commitments.
Mapping a process is the first step to take to examine the process and determine where and why important faults occur. To carry out a process mapping, it is necessary to capture it in a Flow Chart following the following points:
- Identify the “Key” process and assign it a name.
- Identify the most important functions involved in the process through a list of left side of the map.
- Identify the starting point by representing it on the upper left side. Moving down and to the right enter the activities associated with each participant.
- Connect activities through an arrow from the provider to your client more righ now.
- Identify the measurements that exist for each exit once the Mapping.
Although there are dozens of specialized symbols used to make the Flowchart, the used most frequently are those shown in the following image:
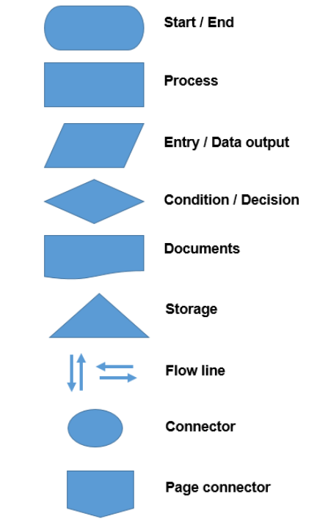
Process Mapping allows to obtain:
- A means for the Teams to examine the Processes.
- A focus on the connections and relationships between the work units.
- An overview of all the steps, activities, tasks and measures of a process.
- Understanding how various activities are interconnected and where they might be failing the connections or activities.
Philosophy Lean Manufacturing
Lean Manufacturing has its origin in the Just in time production system. Lean Manufacturing consists of the systematic application of a set of techniques in search of improvement of the productive processes through the improvement of times, optimization of the plant distribution, quality, reduction of all types of waste -which we will define as the processes or activities that use more resources than strictly necessary- among others.
Lean Manufacturing is a work philosophy based on people, The key to the model is in generate a new culture that tends to find a way to apply improvements at the level of job as a production line, considering collaboration and communication between managers, managers, and operators, that is, to fully involve all members of the organization, the main problem for its implementation is the lack of managers’ conviction about the results they can obtain, the resistance to change by part of the workers and the lack of leadership.
It has its foundations in a culture of “analyze, think and act” deployed from the experience of
the people who are in direct contact with the problems, define the way of improvement and optimization of the production system aimed at identifying and eliminating all types of waste (focusing on seven principals).
To achieve its objectives, it systematically applies a set of techniques that cover jobs, internal production flow supply chain management, up maintenance and quality management. Its final objective is to generate a new culture of improvement in business organization, based on communication and teamwork, looking for continuously new and more agile ways of doing things.
Lean is not only applied in manufacturing companies, but in all types of organizations. To the about 60% of the costs of a product or service can be attributed to the administrative area of the processes. That is why the principles of Lean are being applied with great success in many departments of companies from different industries equally with the objectives of eliminating waste and reduce costs. It is important to mention that the Lean Manufacturing philosophy does not Its objective is to eliminate people, but to use them in the most efficient way.
JIT (Just in Time)
Is a philosophy that defines the way in which a production system should be optimized, it is about delivering raw materials or components to the manufacturing line so that they arrive just in time as they are necessary. This results in a capacity of the company to deliver the product to the market requested, in a short time, in the required amount.
The JIT has four main objectives:
1. Point out the problems: think of the Japanese analogy of the river of stocks. The level of the river represents the inventories (stocks) and the operations of the company are visualized as a ship navigating the same, when a company try to lower the level of your inventories discover rocks, that is, problems. When these problems arise in companies, the typical response is to increase the levels of inventories to cover the problems. In contrast, the philosophy of JIT indicates that when problems appear must be addressed and resolved, the level of inventories can then gradually reduce until you discover another problem that must be resolved also and so on.
2. Eliminate waste: the objective is to eliminate activities that do not add value to the product to reduce costs, increase quality and increase the level of service to client. In order to identify and eliminate waste, you must first define what are and what each one of them consists of As mentioned earlier, the Lean philosophy focuses on seven main waste, which are:
- Overproduction: production of some type of work before it is required or simply produce more than the amount needed or requested by the customer, not generates added value. Some examples of this waste in processes transactions are to send the same document more than once by e-mail, more analysis than necessary or make reports that will not be used.
- Waiting time: dead times between phases or productive activities by lack of coordination or materials not available, leads to no flow I continue in the process. Examples of this type of waste in the office are expect some kind of approval, delays in obtaining or sending the information.
- Transportation: unnecessary movement of people or resources between activities, such as traveling the office several times to take documents to another department, move and / or update information in different systems.
- On processing: work more than necessary on a piece or re-work on defective parts, resources and time are invested and the client will not pay for them since they do not add value. Some examples of this waste are duplicating reports, enter the same information several times, correct wrong information captured.
- Inventory: goes hand in hand with overproduction, when materials are stored premiums, finished product or in process increase costs since it is required of space and time of someone and in the end do not add any value. Stacks of papers, Work on hold or calls on hold represent this type of waste.
- Movement: unnecessary movements of people or resources within the jobs, any type of movement that does not add value is considered a waste. Search for any document in archives not organized or walk to the copier are examples of movements like waste in the office.
- Defects: they are badly processed pieces due to not doing things correctly from the first time, these pieces end up being discarded or re working which leads to an increase in production costs. The most common examples are the capture or entry of erroneous information, as well as make mistakes when entering information that will have to be corrected (re worked) later or even the loss of information.
3. Simplicity: is based on the fact that it is very likely that simple approaches lead to more effective management. Reduce the delay times in the flow and remove obstacles in the process leads to a continuous movement of the product / service (flow continuously). A simple approach to the flow of material is to eliminate the routes complex and look for more direct flow lines, if possible unidirectional or group the products in families that are manufactured in a flow line.
The application of the flow generates a faster and more accurate response with less effort and less waste. It allows to produce only what the client requests and avoids the generation of a unnecessary inventory.
4. Establishment of systems to identify problems: establish mechanisms for identify the problems at the time they are presented, they must be thought of in a that some type of warning is triggered when a problem arises.
These four objectives can be summarized in what is called “Theory of five zeros”:
- Zero time to the market
- Zero defects in the products
- Zero time losses
- Zero work paper
- Zero inventories
The work must be constant to achieve shorter production cycles, focusing the
efforts in the value for the client and eliminate waste, “No machine or process will reach a point from which you can not continue to improve”.