This article aims to dissect and facilitate the analysis of the five core lean principles. The principles that will be focused on, were originated by the Lean Principles Institute.
Organizations aim to continuously improve, and the lean mindset is something that tends to be adopted as employees enter a workforce, and not something that is directly taught to most professions, unless they have some sort of industrial engineering background. Most engineering professions learn lean principles later on in their job execution.
Image 1. The Five Lean Principles
The Lean methodology of thinking is an ideal means via which processes in the service or manufacturing industry can be optimized. Various sectors ranging from service sectors such as hotels and hospitals, have adopted the lean methodology.
Lean, as the name suggests, is a waste elimination mechanism, which allows organizations to run in their zones of maximum efficiency. Once in this state, the maximum profitability of an organization can be achieved. The applications of lean are numerous in all organizations. The aim is to have a smoothly running, well integrated enterprise.
The five principles of Lean have been represented pictorially, in image one above. We will analyze them in detail below.
1. Value
During the lean process, the voice of the customer is determined. This usually involves a meeting where both the customer and supplier identify what quality means. For a product being delivered, quality can be dissected into various measurable components.
Alumina refineries and smelters establish relationships with each other. The smelters, as customers create a requirements list, and identify what parameters and their values are critical to efficient operation. There is a rating system that determines how satisfied the customer will be if product specifications are delivered within particular ranges.
The supplier then assesses their process, and identifies if they can deliver those requirements. If there is a match, the suppliers objective with each delivery, is to ensure that the customer requirements are being met.
In the service industry, similar standards requirements are also being upheld. When cleaners clean a room, there is a checklist of items that they are required to ensure is complete. These requirements are as defined by hotel guests, who have determined what cleanliness means to them.
Value can also be measured in terms of the cost of a product or service.
2. Value Stream
The value stream is the series of steps and processes needed to be executed, in order for a product or service to be delivered to the customer. In Lean, the process of value stream mapping is a pictorial representation of this process.
What it entails is a surface breakdown of each step of the process, in a recipe like manner, which if followed by a layman will lead to the final product. Value stream mapping is a key baseline to all process operations.
If any opportunities are identified in the process…downstream corrective action can then be taken. It helps to have the value stream map readily visible the relevant departments, so that quick references can be made to a process.
3. Flow
Flow management is ensuring that the smooth process operations are being upheld, the majority of the time. Allocations for downtime can be made to facilitate occurrences like maintenance but outside of that barring any unforeseen circumstances uptime should be at peak in order to maximize production or service. Careful system assessment will identify bottlenecks so that the critical process optimization steps can be implemented to facilitate the maximum flow.
4. Pull
The customer is always king. Additionally, as organizations strive to lower their costs by lowering inventory…there is a general drive towards a just-in-time process. These process ideally have no buffer, but real world organizations do require buffers. No process is 100% perfect, and you’ll need back up in order to progress.
With a just-in-time process, customers will receive products soon after ordering. With an optimized supply chain…the relevant items, in the right quantities will be delivered…without any excess backlog, or inventory in process. This is a major cost saver in many manufacturing plants today.
5. Perfection
Perfection is that optimization step that makes each process iteration better. Every time you do something…you get better at it, provided that at each iteration, the previous mistakes were not repeated. Perfection activities include kaizens, which identify opportunities, and aim to fix them either on the spot, or as soon as possible.
With the steps above implemented, process improvements are guaranteed to be experienced and the optimized lean way of operating become standard in your organization. Operational Excellence is fast becoming the way of life for all modern organizations in the service and manufacturing industries.
Cost of Quality
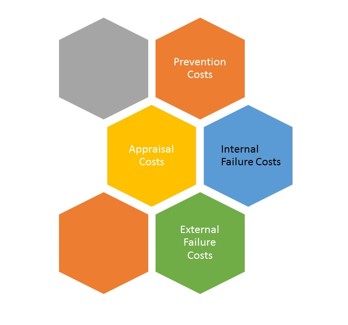
Cost of Poor Quality is a collection of operational losses that is associated with the provision of poor quality products or services. In some instances, the customer will either outright reject the product, leaving the organization to either scrap or rework the product, or will accept the product at a reduced price.
Regardless of the outcome, it is not in the best interest of an organization to be losing money, which is why identifying and eliminating the root cause of quality losses will be critical to an organization’s operational improvements.
The Lean Methodology of thinking has identified four major sources of losses in a functioning operational system. These losses will be analyzed below, in this article’s assessments. The cost of poor quality is a lean methodology which measures the impact of these operational losses.
Once the opportunity losses are quantized, an organization can then take the steps to reduce the losses according to the order of magnitude. The four types of losses which will be assessed are highlighted below:
Prevention Costs
There is a saying that states that prevention is better than cure. There are some instances where Quality Management System design has built in costs that will ensure that once the system is implemented, downstream losses are avoided.
It is the classic case of preparation ahead of the anticipated challenge. Utilizing a system such as ISO 9001: 2008 and the subsequent series is an appropriate means via which prevent costs can be prevented. The system itself, with the built in PDCA cycle, covers all the aspects of Quality Management that are necessary for the system under consideration to thrive.
Appraisal Costs
Lean project management incorporates a monitoring and control phase to ensure that the system under consideration remains in control and capable. Appraisal costs are associated with process management and include procurement assessments, downstream quality assessment along the process, and prior to customer delivery. Critical processes involved in appraisal include the verification processes, Quality Audits (built into ISO) and Supplier ratings via an established procurement system.
Internal Failure Costs
If there’s a system failure, and quality defects are identified…the products or services must be either scrapped or reworked. The costs associated with these two processes account for internal failure costs.
Organizations with built in quality systems will usually detect these failures before delivery. As a result systems to facilitate waste, scrap, rework, and failure analysis are the ideal preventative systems to incorporate into the organization’s operations. Prevention is better than cure, so seeing the issue ahead of time, will prevent down stream challenges with the customers.
External Failure Costs
External failure costs occur after the fact. Due to a breach of the quality management system, products can reach the customer in a substandard fashion. Appropriate systems such as repairs and servicing, warranties, complaints systems and product returns work well to ensure that customers are satisfied after the initial disappointment.
Most customers are not unreasonable, but the best advice from retail that can apply to all organizations is that the customers must be doubly assured that all will be well, once the breach has occurred.
Cost of poor Quality as an operational loss, cannot be underestimated. In many instances, the costs incurred due to poor quality in one area, can actually span entire supply chains. One very vivid example is in the case of alumina refining. Alumina quality is influenced primarily by the amount of silica in the finished product.
Silica, being a glass affects the melting point of aluminum metal once the alumina is fed to smelter pots. If too much silica is present in an alumina batch, the electricity costs of a smelter can skyrocket. In order to protect themselves, smelters will go out of their way to avoid poor quality alumina.
For a refinery who finds themselves in a position where their product is rejected, they could be left with a waiting ship at port. A waiting ship has other locations on their schedule. If they miss their next location, due to waiting on a shipment, an organization will be charged for demurrage.
Regardless of the outcome, it is not in the best interest of an organization to be losing money, which is why identifying and eliminating the root cause of quality losses will be critical to an organization’s operational improvements. Applying the Cost of poor Quality Methodology is a sure way to ensure that all remains well with an organization, and good customer-supplier relations are upheld.