After gaining much success in the manufacturing sector, Lean has found widespread applications in benefiting the Healthcare sector. The primary intention of all Lean Operations is to minimize the resources needed to facilitate the accomplishments of a customer’s desires.
This is facilitated via the Lean cycle, which carries an organization through its value stream, in order to ensure that all activities are being executed efficiently. In the Healthcare Sector, various jurisdictions inclusive of the United Kingdom, Australia and Canada have successfully applied Lean principles to their Operations Strategies. Applied in a holistic fashion, the appropriate organizational transformations can be achieved.
In the Healthcare sector, Lean’s primary objectives are to improve patient care and maximize value. This objective is via the process of eliminating wastes in the system, as well as the wait time associated with being hospitalized.
This article will discuss two critical Lean Operations Tools, which have proven to be effective in Healthcare Management. When it comes to hospital systems, it is important for the entire team to be on the same page, so that the system has a chance to flourish in an appropriate manner.
Value-Stream Mapping has proven to be an effective tool, for a visualization of a hospital system. This can include individual departments or the entire organization. The key is to identify the key sources of information and materials flow. Appropriate process flow maps, once developed, can identify opportunities for workflow management and optimization.
Critical to healthcare is interdepartmental transitions. Delays can affect patient recovery, so ensuring a smooth transition where necessary, can improve an institution’s standard of care.
How to Create a Value Stream Map
The first step is to ensure that the process under surveillance is properly assessed. This can include an individual procedure such as a surgery, or a process such as a patient admissions process. Once each step is identified, then an appropriate step by step visual will then be recommended, so that the process itself can be visualized.
This is best initiated on an A3 sized paper. Once mapped out, critical information such as waiting times can be identified, and the critical improvement tools implemented to facilitate the change.
Continuous Improvement – PDCA Cycle
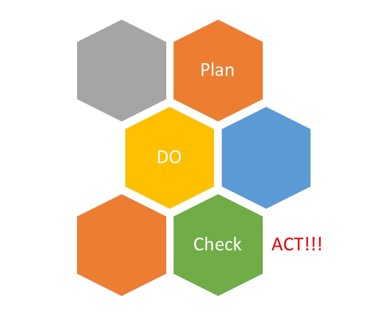
Continuous Improvement Activities when executed in the Healthcare Sector, will enable an organization to optimize its operations and become a better supplier to its patients. The industry is always challenging itself to improve its quality of care.
In any healthcare institution, there is a drive to be the best there is, because other similar entities are after the same target. Providing the highest patient care for the lowest possible price, is the primary purpose at the end of the day.
With customers being as fickle as they are, and with the advent of alternate health care strategies such as natural methods, or cheaper external services, local hospitals must do the best they can to ensure that they are continuously improving their delivery.
Continuous Improvement is a part of the Plan-Do-Check-Act (PDCA) Cycle that is inherent in Lean and Six Sigma Processes. Plan-Do-Check-Act is born out of the ISO movement, and is geared at ensuring that organizations have appropriate mechanisms in place to satisfy their customer in a measurable way.
Healthcare organizations are not exempt from this cycle. As organizations strive to keep improving, the actions involved in continuous improvement provide that marginal change that keeps an organization at the cutting edge of the industry.
From the A3 and value stream map highlighted above, in day to day operations, healthcare based organizations will benefit from having a daily management system, which allows them to track the performance of critical targets. If there are any deviations from target, the relevant changes can then be made.
Via incremental implementation, starting with the Value Stream Map above, and then building out the system in order to facilitate the appropriate PDCA implementation, an appropriate feedback loop will be developed, where appropriate process changes can be integrated into an organization’s operations in order to facilitate the key target of satisfying customers at the appropriate price point.
It’s an interesting challenge in healthcare, and with the implementation, many entities have achieve their desired organizational outcomes. Since our health is our wealth, Lean operations guarantees the appropriate delivery of that desired outcome.