Lean Manufacturing methodology was started by Taiichi Ohno at 1950s under the name of Toyota Production System (TPS). It started after a visit of Eiji Toyoda to Ford’s facility located at Rouge (US).
By that time, economic reconstruction of the countries that participated in World War Two evolved on different ways: meanwhile US required of continuous and huge production volume, for example, Ford’s principle of mass-producing the same automobiles in large production runs, post war’s Japan required small quantities of cars to be produced in many varieties.
However, this philosophy was not in the scope of Japan’s manufacturers nor all over the world by two decades. It was not until oil crisis in 1973 that other Japanese firms realized about its existence. Since then, TPS has been studied, copied and implemented across many industries.
Term that we currently recognize, Lean Manufacturing, was coined in 1990 in the book The Machine that Changed the World by Womack, Jones and Roos. They described results of a five-year study into the automotive industry
Almost 70 years later, Lean Manufacturing is still referred as a radical departure from traditional operations practice.
In 1998, Ohno described that the most important objective of the TPS is increasing production efficiency through consistently and thoroughly eliminating waste. On the other hand, traditional thinking says that in order to increase efficiency you need to work more, faster or harder, and as a consequence, you need to increase people or equipment to achieve it.
Lean Manufacturing is focused on assuring all activities you perform are value-added. A simple way of defining this is anything that a customer is willing of paying for. So, in all the activities or tasks you do in order to give the final customer a product or a service, you need to identify all these non-value-added activities and then working on eliminate them or, at least (because, unfortunately, there are non-added-value activities that are impossible of eliminate them) make them work efficiently.
Waste may be defined as any activity that adds no value but consumes resource. Ohno described seven wastes. Below table shows definition as well as simple examples you may find in healthcare:
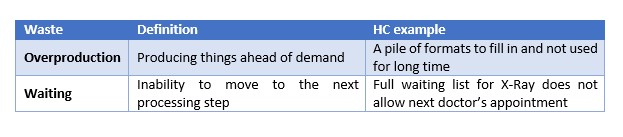
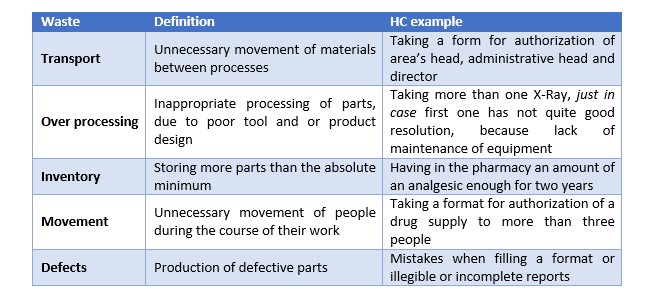
In a simple way, implementation of lean manufacturing consists in applying a series of methodological tools in order to effectively identify and eliminate waste. This is achieved by creating a Value Stream Map (VSM) of current process and then create the desired state map. Then, an action plan is defined and followed. This requires a hard team work from all levels in the organization, since top management to first levels.
Even Lean Manufacturing is not a new methodology, healthcare started looking at it by 2000s. Since then, success cases have been compiled and published. We will comment some of this cases and at the end of this blog I am letting some references for further information, which can even been searched at PubMed.
Virginia Mason Medical Center, in 2004, reduced 53% its inventory and set up time in 82%, after a two years lean discipline.
ThedaCare, Inc., in 2004, saved $3.3 Mi, and also reduced in 50% clinical paperwork time in admission.
In 2011, Washington University School of Medicine decreased door-to-needle times and percent of patients treated ≤60 minutes from hospital arrival were improved in the post-VSA epoch: 60 minutes versus 39 minutes.
In 2012, in a Swedish pediatric Accident and Emergency department improved waiting and lead times in 19% and 24%. These were achieved and sustained in the two years following lean-inspired changes to employee roles, staffing and scheduling, communication and coordination, expertise, workspace layout, and problem solving.
As it can be seen, there are multiple benefits when Lean manufacturing is implemented. Nevertheless it was born for an automobile-manufacturing firm, its demonstrated universality brings a lot of benefits when is implemented and followed.
More success cases are available for review at Internet, so, what are you waiting for? Starting thinking lean!
References and recommended links
- Going Lean in Health Care. IHI Innovation Series white paper. Cambridge, MA: Institute for Healthcare Improvement; 2005. (Available on IHI.org)
- Lawal et al.: Lean management in health care: definition, concepts, methodology and effects reported (systematic review protocol). Systematic Reviews 2014 3:103.
- Application of lean methods improves surgical clinic experience, Journal of Pediatric Surgery, July 2010, Volume 45, Issue 7, Pages 1420–1425.
- Ford, et al.: Reducing Door-to-Needle Times Using Toyota’s Lean Manufacturing Principles and Value, Stroke. 2012;43:3395-3398; originally published online November 8, 2012; (available on http://stroke.ahajournals.org/content/43/12/3395)
- Mazzocato et al.: How does lean work in emergency care? A case study of a lean-inspired intervention at the Astrid Lindgren Children’s hospital, Stockholm, Sweden. BMC Health Services Research 2012 12:28.