LEAN Engineering is a work philosophy, based on people, that defines the way to improve and optimize a production system focusing on identifying and eliminate all kinds of “waste”, defined these as those processes or activities that use more resources than strictly necessary.
Identify several types of “waste” that are observed in production: overproduction, time waiting, transportation, excess processing, inventory, movement and defects. LEAN looks at what we should not be doing because it does not add value to the client and it tends to eliminate it.
To achieve its objectives, it deploys a systematic and habitual application of an extensive set of techniques that cover practically all areas manufacturing operations: organization of jobs, quality management, Internal flow of production, maintenance, management of the supply chain. The benefits obtained in a LEAN implementation are evident and demonstrated.
Its final objective is to generate a new CULTURE of the improvement based on the communication and teamwork; For this it is essential to adapt the method to each specific case. The LEAN philosophy takes nothing for granted and searches continuously new ways of doing things in a more agile, flexible and economic way.
LEAN Engineering is not a static concept, which can be defined directly, nor a radical philosophy that breaks with everything known. Its novelty consists in the combination of different elements, techniques and applications arising from the study on foot machine and supported by the management in the full conviction of their need. LEAN thinking evolves permanently as a consequence.
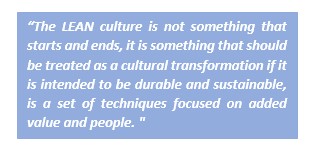
A company with a successful track record in production rationalization methods is in an excellent position to experiment with the LEAN method by adopting new approaches, selecting those specific techniques and principles that best suit your productive system, product and human team.
The Culture of Engineering Excellence
The dissemination of LEAN management techniques has been accompanied by the concepts of “excellence in engineering” or “world class company”. The knowledge of objectives that imply these concepts is very convenient in order to start in the new techniques, key to the competitiveness of companies. From the point of view of “excellence” companies that want to compete successfully in the current market. The following objectives should be considered:
1. Design to “manufacture”.
2. Reduce machine preparation times to increase flexibility and decrease the execution deadlines.
3. Achieve a distribution of the plant that ensures a low inventory, minimize trips and facilitate direct control by visibility.
4. Use technology to reduce the variability of the process.
5. Make it easy to manufacture the product without errors.
6. Organize the workplace to eliminate search times.
7. Train workers to facilitate motivation, versatility and multidisciplinarity.
8. Ensure that line personnel are the first to try to solve problems.
9. Conserve and improve existing equipment before thinking about new equipment. Use intensively preventive maintenance involving all employees.
10. Increase the frequency of deliveries of products.
11. Ensure that failure detection is carried out at the source, creating mechanisms simple ones that immediately detect the problems.
12. Ensure that all people are regularly informed about the needs of customers, their degree of satisfaction and the methods to be used for their satisfaction.
LEAN Engineering techniques are the ideal roadmap to achieve turn a company into competitive and of excellence within the current market.
Structure of the LEAN system
LEAN is a system with many dimensions that affects especially the elimination of the waste by applying the techniques that will be described in this article. LEAN is a cultural change in the business organization with a High commitment from the company management that decides to implement it.
In these conditions it is complicated to make a simple scheme that reflects the multiple pillars, fundamentals, principles, techniques and methods that it considers and that are not always homogeneous taking into account that terms and concepts that vary are handled
according to the source consulted. Indicate, in this regard, that academics and consultants they do not agree when it comes to clearly identifying if a tool is or do not LEAN.
Traditionally, the scheme of the “Production System House” has been used Toyota “to quickly visualize the philosophy contained in LEAN and the techniques available for your application. It is explained using a house because it constitutes a structural system that is strong as long as foundations and columns be; a part in poor condition would weaken the entire system. Figure 1 represents a updated adaptation of this “House”.
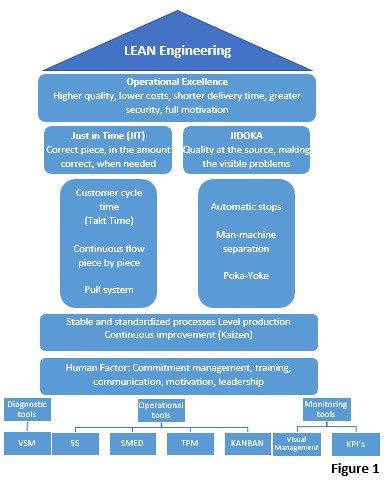
The roof of the house is constituted by the goals pursued that are identified with the better quality, the lowest cost, the shortest delivery time or maturation time (Lead-time). Holding this roof are the two columns that support the system: JIT and Jidoka.
The JIT, perhaps the most recognized tool of the Toyota system, means producing the indicated article at the required time and in the exact amount. Jidoka is about giving machines and operators the ability to determine when an abnormal condition occurs and immediately stop the process. That system can detect the causes of the problems and eliminate them at the root of that the defects do not pass to the following stations.
The basis of the house consists in the standardization and stability of the processes: the heijunka or leveling of production and the systematic application of continuous improvement.
The human factor has been added to these traditional foundations in the implementation of LEAN, a factor that manifests itself in many facets such as are the commitment of the management, the formation of teams led by a leader, the training and training of personnel, motivation mechanisms and systems of reward.
All the elements of this house are built through the application of multiple techniques that have been divided as they are used for the diagnosis of the system, operational level, or as follow-up techniques.
It is important to use this scheme flexibly in a first approximation to the LEAN thinking. While the Toyota House is a good exercise at the presentation level formal, a first vision can induce a manager to think that it is a system difficult to understand, complicated to implement and long to implement. Nothing else far from reality.
The scheme is a way to transfer all facets to paper of the system. Each company, based on its characteristics, experiences, market, staff and objectives, both in the short and medium term, must draw up a plan of implantation with limited objectives; selecting and implementing, step by step, the most appropriate techniques.