The oldest and most widely used inventory system in the world is the point of reposition (POR) system.
The simple rule of the point of reposition says the following: When stocks go down, more is asked. Even squirrels follow that rule to replenish their stocks of nuts. But the POR results in a lot of inventory. More parts and raw materials are requested to comply with the rule, rather than by necessity.
Manufacturers who use POR do so because they have difficulty associating the need for parts with the final product program. The planning of necessary materials (PNM) is a better way, since it takes advantage of the capacity of the computer to make thousands of simple calculations in order to transform a master program of final products into the quantity of necessary parts. But like the POR, this method is oriented towards the lot; that is to say, the computer collects all the orders of a certain number of part of a given period and recommends that the number of parts in a lot of good size be produced or bought.
The companies that resort to the planning of necessary materials order by lots, instead of piece by piece (just in time), because they have not reduced their preparation times so that the small lots are economical. If they did, the logical choice would be a simple manual kanban, instead of this complex, expensive and computer-based system. The paradox of the PNM is that, if the company eliminates the obstacle of the preparation time so that the PNM is really effective to radically reduce the inventories, the PNM will no longer be necessary; the preferable the kanban.
The point is set forth in terms of the “Fundamental Factor”. The PNM correctly calculates the needs of parts associated with precision with the master program of final products. But what is correct at the time of calculation is subject to error later.
The cause is that the lots are substantial and the time in advance to produce is long, from one to several weeks.
During this time there will be delays and changes of programs, so that the batch that is being produced is no longer correct in relation to the master program of final products.
The size of the lot and the time of production deteriorate the close association between the quantity of necessary parts and the programs of final products.
Similarities and differences of inventories
Below, a diagram is developed, where the main similarities and differences of the inventories that have been the object of our analysis are appreciated.
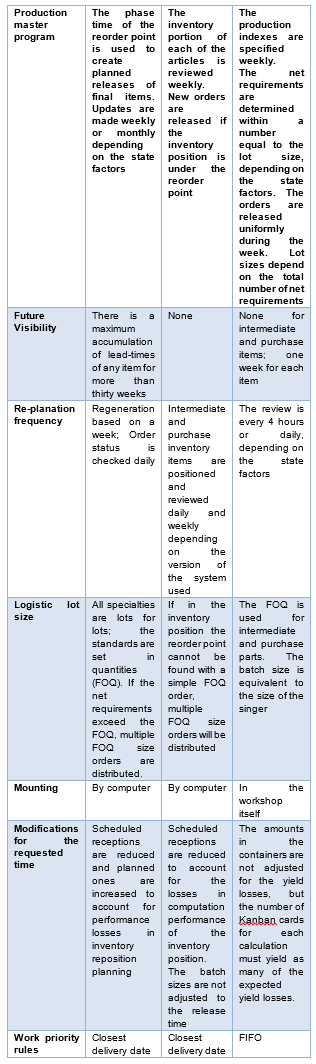
How does the Kanban circulate?
The kanban circulates in the following way:
- When the necessary parts of the assembly line are to be used first, a transport kanban is collected and placed in a specific position.
- A worker carries this kanban to the previous process to obtain processed parts. Remove a production kanban from a pallet of processed parts and place it in a pre-set position. The transport kanban is placed on the pallet and the pallet is transported to the line.
- The Kanban of work in process or Kanban of production removed from the pallet in previous process, serves as an order and work instruction card that promotes the processing of semiprocessed parts supplied from the previous process.
- When this occurs, the production card corresponding to the previous process is removed from a pallet of semi-produced pieces and replaced by a transport kanban.
With this system, you only need to indicate the changes of plans at the end of the assembly line.
This system has the added benefit of simplifying bureaucracy, when production is executed by passing instructions to each process, some of them may be delayed, or speculative production may generate unnecessary inventories. The Kanban system prevents this waste.
The production system tries to minimize the inventories of work in process, as well as the stocks of finished products. For this reason, it requires production in small lots, with numerous deliveries and frequent transports.
Work instruction cards and transfer of conventional control processes are not used.
And instead of this, the times and places of the deliveries are specified in detail. The system is established as follows:
- Deliveries are made several times a day.
- The physical delivery points are specified in detail to avoid placing pieces in storage and then having them removed to transfer them to the line.
- The space available for the placement of pieces is limited to make it impossible to accumulate excess stocks.
The movement of the kanbanes regulates the movement of products. At the same time, the number of kanbanes restricts the number of products in circulation. The kanban must always move with the products.