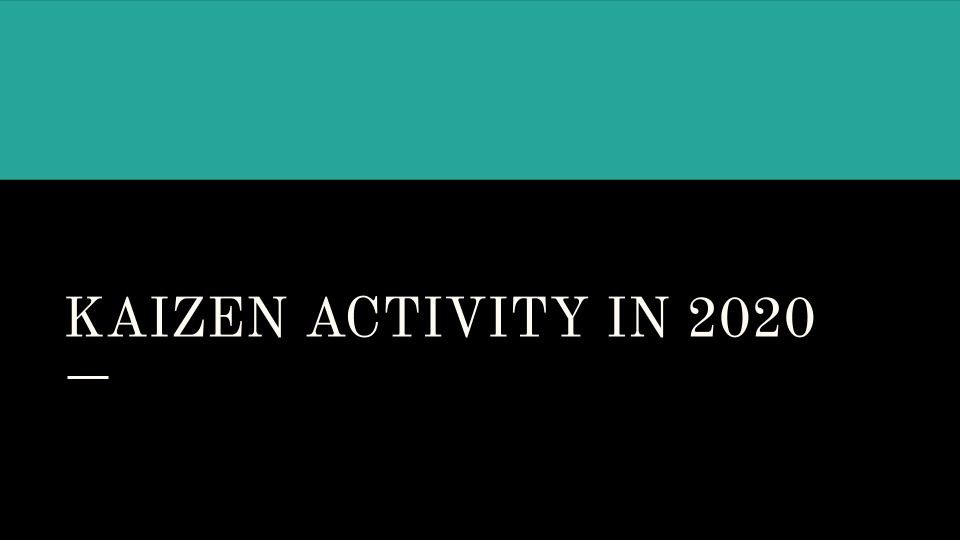
“Never stop investing. Never stop improving. Never stop doing something new. Make it your goal to be better each and every day, in some small way. Remember the Japanese concept of Kaizen. Small daily improvements eventually result in huge advantages.” – Bob Parson
There is a saying that goes…”The more things change…is the more they stay the same”. The industrial plant for the most part, is the epitome of that experience. Day in and day out…you make production. That being the case, it’s often easy for individuals to not realize that the plant they are working in, can grow and evolve with time. Quality standards change, different customers will want different blends of your product and it is always a good idea to pretty much ensure that you are ready.
Within the plant itself, with time systems can lose their effectiveness. Staff can change positions and new members come in and implement their own systems and cause operational shifts. With that said… “How is change maintained in an organization?” With many best practices implemented, one of the best identified ways to facilitate change is via ongoing work. Ongoing change is achieved via the kaizen activity.
Kaizen, is an ongoing activity that is an inbuilt approach to improving operational systems via the eyes of those who work in those systems on a daily basis. Subtle incremental change is always the key to ensuring that your organization achieves its objectives of staying competitive in a marketplace that is evolving.
2020 as a year, is one of the most interesting years that the entire globe has experienced. As a year with more people working from home than working inside their office buildings, the industrial space will somewhat be operating in a similar manner.
How then…will kaizen activity be conducted in 2020? Business must operate and as a result, it will be important for ongoing change to keep taking place. Continuous improvement in 2020 is something that we all need to factor in. On a positive note, we will not be quarantined forever, and those on the front line still have to ensure that they are doing things to keep the plant operations intact.
For those on the shop floor, there is always room to make small improvements and challenge the status quo of your current industrial environment. If you’re at work, you’re essential, so you might as well meet in order to get the place in a state that will facilitate the peak demand once the peak operations resume. In our opinions, the best time to conduct a kaizen activity is in the now.
The plant can actually become your research facility. Knowing that you’ll be operating predominantly at a medium to low flow, you can actually start toggling with the plant flows and identify where your peak operating points are. Without so much pressure, you’ll be able to get things done and your opportunities for improvement will be identified.
Kaizen is a Japanese word for changing for the good. It is always a good idea to believe that everything can be improved. There is no perfect process, and once you approach your plant from that perspective, you’ll actually be in the perfect position to capitalize once the market restores. All you have to do in 2020 is get ready.
The seasons themselves always restore. Farmers always talk about seasons for planting, and then seasons for reaping. Likewise in the industrial realm, 2020 represents that season of global downtime, which are actually presenting us with an opportunity to attain much once the economy resumes its normalcy.
Kaizen will be the key that prepares your industrial plant for the booms to come after the shortfall. Continuous improvements will result in larger changes over time. The key to your success is just ensuring that you are actually getting started in your process. The employees on the front line are the best to bring about the desired change.
THE KAIZEN METHODOLOGY
Kaizen is a philosophy that is applied to the industrial operating flow. Throughout a plant, mass and energy are flowing and the team’s responsibility is simply to ensure that it is flowing at peak capacity. Maximizing your resources will be the key to ensuring that you remain competitive.
Utilizing the Kaizen approach you can identify several tools in your organization that will bring about change. These include:
- Total Quality Management
- Kanban System
- Daily Management
- 8 D Approach
Embedding all of these systems into your operational structure will be key to ensuring that critical gaps in your operational flow are identified. On the day to day activity Daily Management, Kanban and the 8 D approach will work well. Where a critical issue is identified, a longer event such as a kaizen event will then be warranted.
KAIZEN EVENT
Within the lean movement, organizations do have champions that will be able to drive change. Utilizing your change champion, take the time to have a three to five day kaizen event. A kaizen event is a dedicated activity that will ensure that your system is thoroughly assessed, problems identified and an action plan identified for change.
Teams often gather for days, looking at data, walking the field and taking pictures and videos of their operating sites and allowing themselves to feel the plant and how its operating.
First hand experience is always the best that there is. From this exercise, the team will then be able to take action towards ensuring that future operational runs are optimized. If problems can be fixed on the spot during the kaizen, they can be fixed then. There are often spares and equipment in the warehouse that will facilitate the restoration of some problems on the plant.
Larger projects can then be fixed in a Capex project, or scheduled into a major plant maintenance schedule.
KAIZEN BENEFITS
Kaizen as a tools is one that is quite beneficial to an industrial site. With less resultant waste, more satisfied operational staff and a more efficient site, resultant savings can be diverted to plant expansions.