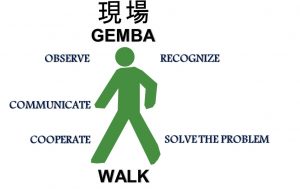
A gemba walk is an almost meditative practice, and requires a specific mindset to pull off. Based on (like so many other modern Lean practices) what was originally a Japanese concept – the word gemba or genba literally meaning “the real place”, though that isn’t the whole concept – it is the idea that direct observation of a work floor is essential to understanding what is really going on there.
While a gemba walk is not a replacement for more detailed data received through other methods (charts and spreadsheets detailing performance and safety violations, that kind of thing) it is an important supplement to that. The idea is that you should walk the floor and simply observe, without any of your preconceptions getting in the way.
That last bit is most important, and harder to pull off than it sounds. Humans all naturally have their own biases, good and bad, it’s how we process the world and the lens through which we filter all critical thought.
Directly observing something, particularly things you may be unfamiliar with except as bullet points on a processes and standards guide, can be an information overload; the amount of sensory information a human can process (consciously and subconsciously) is nothing short of astounding, and a pace as busy as a factory floor can be overwhelming.
It is tempting to, then, try to grade worker performance, viewing how well they follow instructions and the quality of the work they output, but this is a mistake. You should avoid that temptation, and simply let yourself absorb information to be ordered and analyzed later.
So too should you avoid the temptation to mete out punishment for perceived or real flaws, correct mistakes, or interfere in any way with the workday; there will be plenty of time for that later. Making people too aware of your presence, particularly if you punish mistakes interfere too much will make your employees self-conscious and closed off; you will have ruined the entire purpose of the walk, to see things as they really are in the here and now, not try to force reality to be as you wish it to be.
In that regard gemba is more a philosophy than a practice; you must let go of your preconceptions and simply exist in the moment, understanding the ecosystem of your workplace and what everything and everyone’s place in it is.
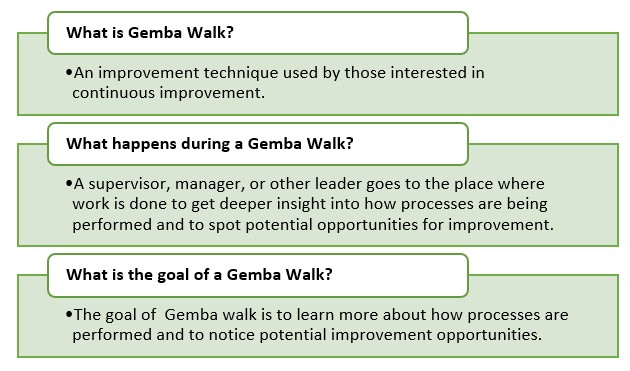
That is not to say that nothing can or should be done with that information, of course. Once you have completed your walk, take stock of what you’ve learned, and supplement it with other information your analysts have gathered.
Think about what you observed, compare and contrast that information with the numbers and data on the page, and then start to work on a plan for improvement; even better, work on a plan to teach those who work under you how to improve themselves, and continue to periodically observe and adjust your approach on subsequent gemba walks.
See how that ecosystem changes with your subtle guiding hand steering it closer to your vision. Then you will have started on the path to kaizen; another Japanese word meaning “change for the better”, in a continuous and ongoing sense. You should always strive to incorporate kaizen into your business, and change can only be achieved if you know where you are now.