1. INTRODUCTION
Job shop scheduling is basically an optimization process in which ideal jobs are assigned to resources at particular times.
Let there be ‘n’ jobs J1, J2, J3…..Jn. Let there be ‘m’ machines M1, M2, M3…..Mn... If below conditions are met, then it is said to be a flow shop sequencing problem.
- The order of sequencing jobs remains same on every machine.
- The order of machine processing every job remains same
- All the job require processing on every machine
The very purpose of flow shop sequencing is to assign jobs to each assigned machines in a manner that the every machines are engaged all the time without being left ideal.
Benefits of flow shop sequencing in organization.
- Improved process efficiency
- Improved machine utilization
- Increased production rate
- Reduced total processing time
- Minimum or Zero Ideal Time
- Potential increase in profits and decrease in costs
2. FLOW SHOP SEQUENCING PROBLEM
Problem: The job sequence needs to be allocated properly to machines in order to minimize the total processing time.
EXISTING FLOW SHOP SEQUENCE
There are 5 jobs, each of which must go through machine A and machine B in the order with processing time given below.
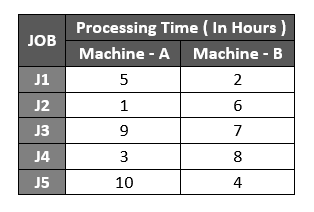
Total Elapsed Time:
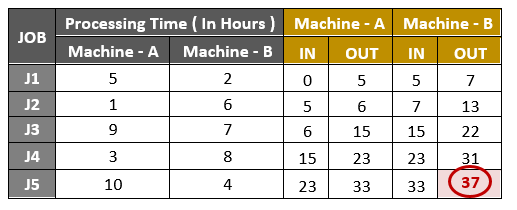
Total Elapsed Time = 37 Hours
Solution: Johnson’s Rule for 2 Machine – ‘n’ job problem flow shop scheduling
STEP – 1: Select the smallest processing Time. In case of tie, select any one of them.
STEP – 2: If the minimum processing time is on First Machine – A, then put the job at the front of sequence. If the minimum processing time is on Second Machine – B, then put the job at the end of sequence.
STEP – 3: Delete the Job for further sequencing
STEP – 4: For the rest of the jobs, again apply STEP – 1 and STEP – 2
STEP – 5: Continue the process till all the jobs are sequenced.
OPTIMIZATION OF FLOW SHOP SEQUENCE
Iteration – 1:
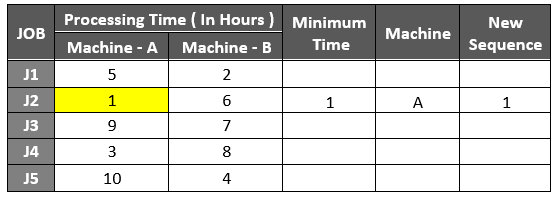
Iteration – 2:
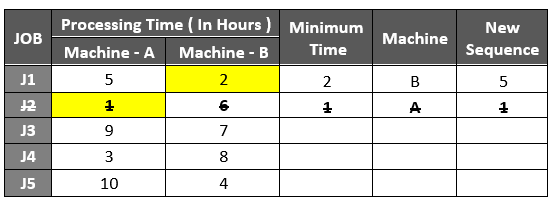
Iteration – 3:
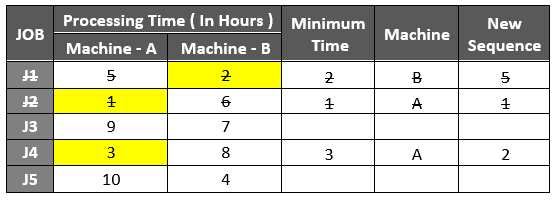
Iteration – 4:
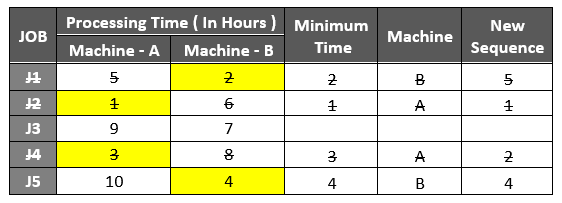
Iteration – 5:
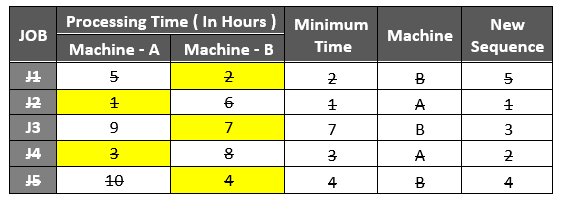
NEW FLOW SHOP SEQUENCE
New Optimal Sequence (Job Number):

New Elapsed Time:
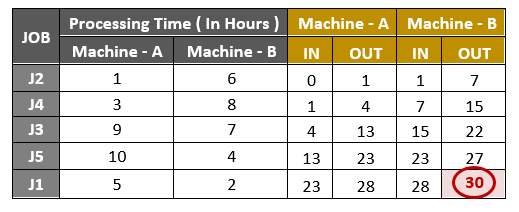
Total Elapsed Time = 30 Hours
Reduction in Processing Time = 37 – 30 = 7 Hours
Percentage Reduction in Time = 7/37 X 100 = 19%.
3. CONCLUSION
With above problem with could clearly understand that with proper sequencing of job and channelization to machines, in above example we could reduce the processing time by 19%. In manufacturing industry it is always necessary to optimize job sequence based on individual workstation so that total processing time can be reduced.