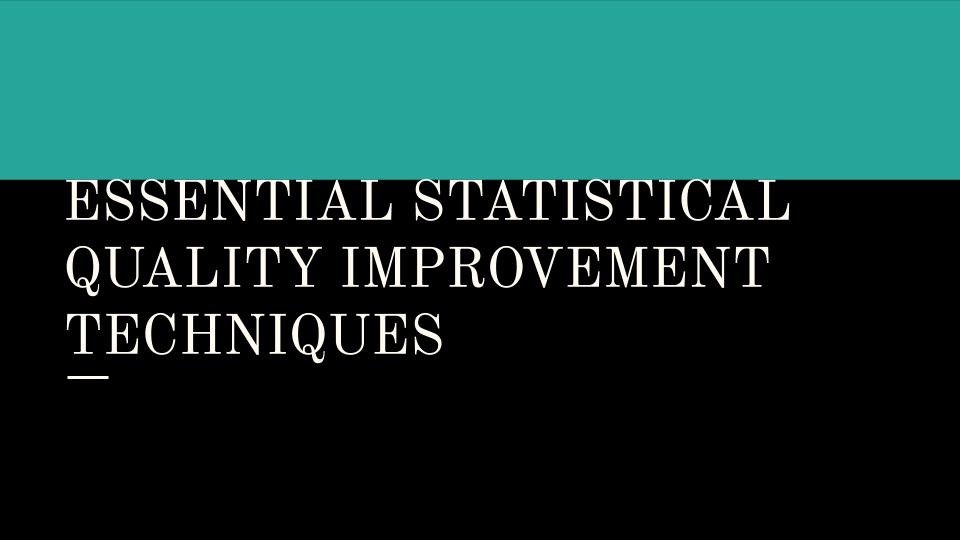
“We must be careful not to confuse data with the abstractions we use to analyse them. “- William James (1842 – 1910, American philosopher and psychologist)
With Industry 4.0 on our hands, all businesses, inclusive of industrial ones are operating with the decisions made from data. Data is the new oil, and it is one of those things that enables us to predict the future, based on activities that have gone beforehand. The advantages of your controls and process engineers is to ensure that you have statistical thinkers within your organization, who can look at your process and equipment performance and ultimately determine what course of action should be taken by the company in order to progress.
An industrial plant is an animated location. With equipment linked to each other, critical process variables such as temperatures, pressures and flows are easily traceable by system control systems. Coupled with the online data systems, industrial plants often have a control lab that will actually sample process fluids and determine if the sensors themselves are stating what they should. Labs validate instruments and ultimately, these numbers that are generated by a facility should be put to good use. By themselves, numbers are numbers. In a good context however, numbers are the key to a plant’s future.
There are many industrial facilities that have servers full of data, yet they don’t know how to use that data to either optimize their facilities, determine if they need to expand their operations or if they are achieving critical process targets. The best companies in 2020 are those who utilize their data to achieve a critical advantage, and enable the management team to make long term strategic decisions that will aid the company to thrive in times of uncertainty.
Quality is met via data, production targets are met via data. That which gets measured…is that which will get managed. Utilizing critical statistical data, will be the key to ensuring that system performance and system capability are met. In the future, companies must ensure that they are making the transition to statistical quality control as a means of system monitoring and control. There are a few statistical tools that will be critical for operations.
STATISTICAL THINKING
For a given process, over time there will be system stability, that will make it possible for the organization to quantify their defects, and implement processes to keep those defects at bay via suitable reaction plans. With the appropriate reaction plans, companies can rest assured that their product quality is of a repeatable standard. Statistical tools exist to facilitate the appropriate analysis of a system. As with all tools implemented in the Plan, Do, Check, Act cycle, there are means via which the percentage of defects to the percentage of acceptable product standards are compared.
The tool of choice for product quality versus acceptance is the Operating Characteristic Curve. Organized similarly to a Gaussian Distribution Curve, the Operating Characteristic Curve is a plot of the Probability of Acceptance (on the Y-axis) to the Proportion of Defects. Organized as a decay curve, the higher the Proportion of Defects experienced by the process or system, is the lower the Probability of Acceptance of the product or service by the organization.
Organizations optimize their systems therefore to facilitate the minimum level of defects in their operations. Chemical Process Systems are ideal examples for the assessment of the different elements of the Operating Characteristic Curve. The first element for assessment is known as Acceptance Sampling. For a production run, assuming a 24 hour day, there will be various elements that result in a process either remaining on its quality critical targets or deviating from these objectives. The aim as an organization is to determine how much variation the organization is willing to accept in order to satisfy its quality standard. The norm is that statistical variation will take place in the production process, so the quality management team of an organization will have to identify the sources of defects, as well as incorporate the appropriate buffers for the change. Acceptance sampling achieves the target of determining the current condition of a system, so that corrective actions can be taken if necessary.
For chemical processes, periodic sampling is implemented. Each shift, a target number of samples can be implemented for analysis. Utilizing graphs containing the target parameter, an upper limit and a lower limit, it will be possible for the system to identify whether or not the current sample is upholding the organization’s standards. If it is, then the process can be left to operate as it normally does. If there’s a consistent trend either upwards or downwards towards the lower end of the range, there is a process discrepancy that is causing a shift. By consistently checking the system, the organization can determine whether or not the system is performing as it should. Sampling is one of the first steps in the implementation of a quality management system.
Depending on the quality management system that the organization is currently utilizing, it is possible to identify certain critical parameters that will determine the system’s status. The Acceptable Quality Level, is utilized in order to identify if the system performance is as desired. Production systems regard re-work as very costly, so it is important for the first operating run to meet the desired target. System averages for the acceptable quality level is a deviation of between 0.1 and 2%. What the system aims to do is maintain between these levels and ultimately sustain the quality level needed in order to satisfy its customers, as well as maintain a normal production run.
With these two parameters in place, the interpretation of the Operating Characteristic Curve is simplified. Using the sampling plan percentages as the X-axis, the customer data will be utilized in order to determine whether or not the product will be accepted by the customer. With zero defects, there will be 100% acceptance, while the odds reduce as we approach the 2% margin.
Systems go to great extremes in order to ensure that their quality is as desired. The quality levels of an organization are usually built into their very operations. Quality standards are established by the customer in a charter that outlines the Voice of the Customer. This charter is then converted into a series of process steps that facilitate the delivery of the customers desires into a tangible product or service. The Operating Characteristic Curve, is the means by which systems can utilize feedback tools to determine if their systems are providing the appropriate standard to their customers.
Statistical tools are always critical to operational performance. Take the time to ensure that you are implementing tools in your operations to achieve your desired objectives.