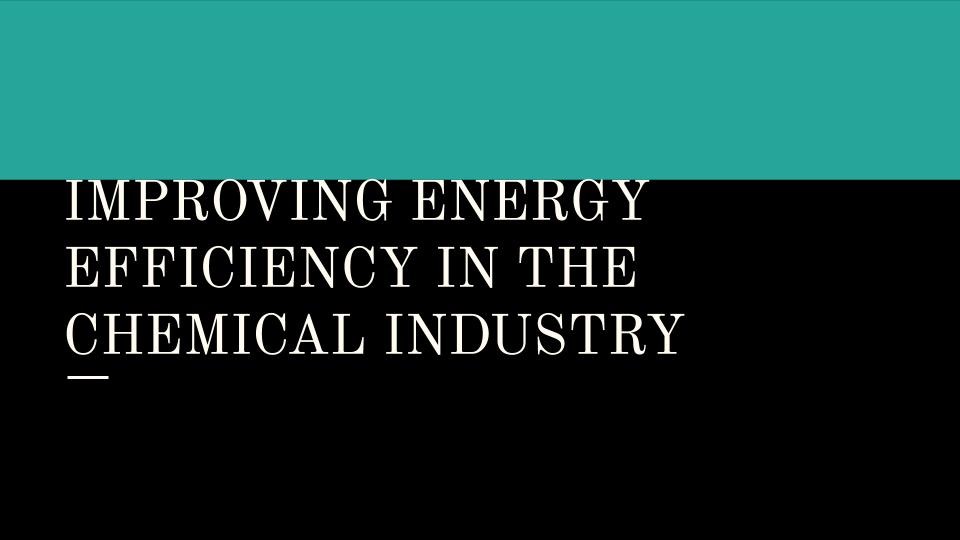
“Moving to energy efficiency and renewable energy powered solutions and factories just makes plain economic sense. We are reducing our [carbon] footprints, powering our factories with solar and wind energy, lowering our overall energy bill, making our products more competitive.” – Harry Verhaar
There is a global mandate that has challenged all organizations to reduce their carbon footprints by the year 2030. The fact of the matter is that industrial organizations are one of the major contributors to the current state of the world’s global warming crisis. The world in 2020 has come to a temporary halt, and interestingly, studies have shown that with the majority of families working from home and homeschooling their children, the cloud of smog that was over most modern cities has actually disappeared.
Within the industrial realm, businesses must operate in order to provide the goods and services that the economy needs in order to stay in motion. Food, Household essentials and other critical items necessary for our household operations come from industrial complexes. With an increased pressure on the organizations to meet the 2030 mandates, one of the most critical factors to include in an operation, is an Energy Management system. A lot of states in jurisdictions like the United States and the EU have taken actions to ensure that industrial energy efficiency is being optimized.
As a start, what many organizations need to take the time to do is ensure that they have a suitable energy project manager, whose sole purpose will be to ensure that system energy requirements are at peak. As a start, Energy Management is a system wide operation that will have to be included in a daily management system. A kaizen or focus plant will enable the organization to determine how they stand with respect to Energy Management.
Energy Management Kaizen
As a start, it will be in the best interest of the organization to ensure that they are in a situation where they have some best practice energy management standards that they plan to uphold. These standards can either be generated in house, or sourced from a standard source such as the ISO. The standard will actually provide the organization with a list of focus areas that the plant will need to focus on. These areas can include:
- Power Generation
- Power Consumption
- Heater Maintenance
- Steam Consumption
- Compressed Air Generation
- Compressed Air Consumption
Each of these activities is a system on its own, and at best it will be in the best interest of an industrial organization to identify how its operations are wagering with respect to the utilization of critical essentials where their energy generation and consumption is concerned. Statistical studies have shown that identifying a current condition and comparing it with a suitable standard, is one of the key ways that an organization can improve its carbon footprint and also save money. As large consumers of utilities whether locally generated or purchased, the anticipated savings of having an appropriate Energy Management system can be up to 10 percent per annum.
A study by the EPA in the United States has indicated that in the industrial realm, the savings anticipated from energy improvements can be achieved predominantly from their electrical efficiency improvements. Via your kaizen activities, you can then place yourself in a position where you can identify the potential savings for your organization.
KNOWING YOUR CURRENT CONDITION
Knowing your current condition can then lead you to identify where you want to be in terms of your energy targets. Key questions to ask yourself include:
How much energy are we consuming right now?
How much does this energy cost us?
Do we know the industry best practice on our utility source?
What will our target be for a complex of our size?
Knowing this information will then inform your system engineers to start identifying your opportunities for improvement. Knowing what your target load profiles should be, will then create a series of action items that each of your departments can then take in order to ensure that they are meeting the critical targets. With an action plan, take your time and work through the items that will be high priority in terms of safety from an energy perspective. For example, if you’re a steam consuming plant, can you save money by ensuring that you fix your steam leaks?
Once that’s finished, you are then in a good position to then tackle the other energy saving initiatives that are more subtle. These can include:
- Installing sensors in your offices that will turn on and off the lights
- Installing variable frequency drives on your motors so that they consume energy according to flow and not just utilize a standard rate.
Knowing all of these as a baseline, will be a critical guide to your Energy Management Initiatives. Start with a kaizen, work towards an action plan and then start implementing.