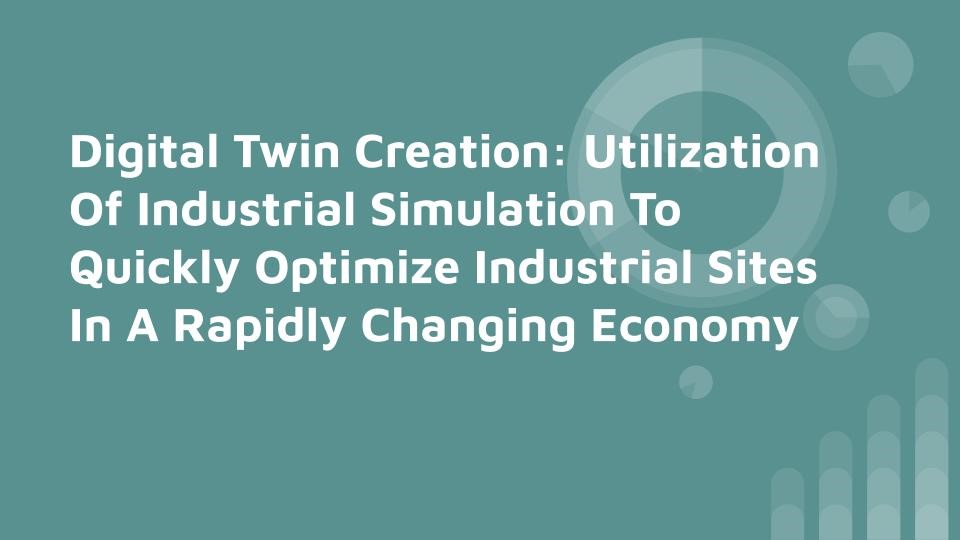
The Cyber-Physical Industrial System is now coming to you soon, via the phenomenon of the digital twin technology. Digital twin technology, is the simulation technology that is able to create a virtual version of your industrial plant, and enable you create what if scenarios before you actually implement a physical change. With the integration of various elements that enable you to change process variables, and determine process outputs, you can utilize existing process data to actually predict your own future.
As a mapping technology, the entire process lifecycle of industrial equipment can be envisioned in a multi-dimensional virtual playing field. As an Industry 4.0 enabler, Digital Twin Technology is part of the wave of the future. There is a history that is associate with all technologies, and it is very important for us to ensure that as an industrial consciousness, we are able to understand the history of digital twin technology, in order to ensure that we can understand how it will fit into our digital future. Industrial research will be made possible via tools like this.
As Computer Aided Design and Simulation continue to evolve, increasing processing power is making it possible to expand on what was started in the 1950’s. With the current ability to generate 3D models, and to provide real time simulation and process scaling, the plant can truly be visualized before it is created. The functionality will enable modelling of manufacturing lines from input to process output, and can generate multiple operating scenarios that will facilitate process optimization. Digital twins are expected to surpass their predecessors in the existing software packaging in less than five years. Anticipated process improvements are up to 10% in production efficiency. Digital Twins will save a lot of time and money for the industrial organizations that do integrate them. What are some of the advantages of of a Digital Twin System?
The Digital Twin System is a means via which organizations can utilize technology to optimize their systems. Organized as a central system that is able to collate and process data, the system provides the appropriate process management teams with feedback on the system’s performance where resource utilization is concerned, and can also be used to forecast future scenarios. Process Engineers focus on various operational and innovative functions during the organization’s optimization process. Visualizing the future will be a great way to see what will benefit the company.
With an appropriate feedback loop, process engineers are able to identify which aspects of their operations are under, over or appropriately utilized. Competition is always a concern for any thriving organization, particularly during a pandemic. Competitive Advantage is a moving target, and cost optimization will always be a tool that the organization’s management can utilize in order to facilitate its core operating objectives.
The various facets of a Digital Twin system include the process analysis tools, automation enhancing tools and IT systems that form the backbone of all organizations systems operations, as well as the supply chain management tools. With appropriate strategic utilization, the organization will facilitate its smooth operations. An appropriate investment in the best Digital Twin system, will guarantee organizational success. You want to measure twice and cut once, especially in these times.
While the benefits of implementing Digital Twin systems outweigh the challenges, there are a few considerations that the organization will need to be wary of while the system is integrated into the operations. Automation of any system is always a challenge, so previous knowledge of the pitfalls will facilitate a smooth transition.
The Implementation Process
Deciding to implement a Digital Twin system is always a major decision for any organization. With appropriate system and process analysis however, it is possible for the organization to determine the best strategy that works for them. It has long been proven that computers optimize systems way better than human minds can process, and as a result, a suitable competitive advantage will be gained by the use of such systems. Previous case studies have shown that the transition to a Digital Twin system can stress employees with new information. With a new system, as well as other challenges to keep the organization running during a pandemic, it is of the utmost importance that organizations make the transition as smooth as possible. An appropriate strategy is a phased implementation, so that the stress of change will not be a shock to the organizations.
The Digital Twin’s purpose is misunderstood
Many organizations are of the impression that simply throwing technology at an organization will solve its problems. The technology is simply a tool, and in some instances it is possible that the Digital Twin system might not be the appropriate solution. Usually, when decisions like this are made, a collective consult will be determined by the organization. Using Six Sigma systems such as a focus plant, a detailed system walk through can be prepared. Once the audit is executed, then the management and their consultants will compare the existing system needs, to the needs that will be met by the Digital Twin system. If there is a mismatch, the Digital Twinsystem will be eliminated, if there is a match of needs to the Digital Twin system’s provisions, then the system can be implemented.
An Appropriate Implementation Plan
It is quite possible to have the right plan, but there may be challenges along the way of implementation. Digital Twin optimization projects are large scale in nature and it will be important for the plan to be realistic and detailed, and well managed along the implementation process. High level project management will be important, as well as the detailed tracking of the process as the plan is being implemented. Many organizations have challenges with this phase of the process. Because so much deliberation is taken in the first instance, once the implementation phases arrive, there is often a loss of steam and the ambitious plan can be missed. With the right motivated personnel, the project management will proceed effortlessly.
The Customization Factor
When custom making anything, there is always an extra element of time to be factored into the plan. Since organizations differ, unless the system in operation is a franchise, there will often be an element of adjustment and scaling that the system developers, as well as the project managers will have to factor into the plan. Designing the system will take time, as well as implementing and training the persons who will use the system to optimize it fully. Many systems are over designed, and employees can be overwhelmed by the various facets of the system such as the user interface, analytical tools etc.
The list of possible challenges can be exhaustive, but the onus is on the organization to ensure that it has a plan that is suited to its own operations. With the right Digital Twin simulation package, all the appropriate system baselines will be easily accessible and the management will appropriately identify what options work best for them in their leadership of the organization.
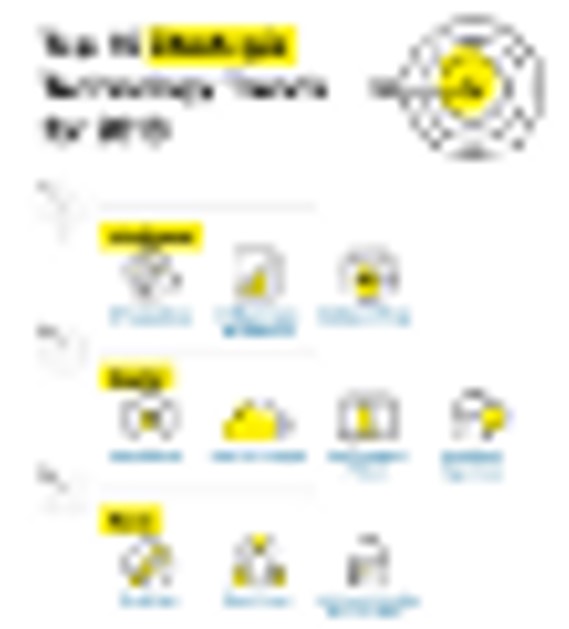
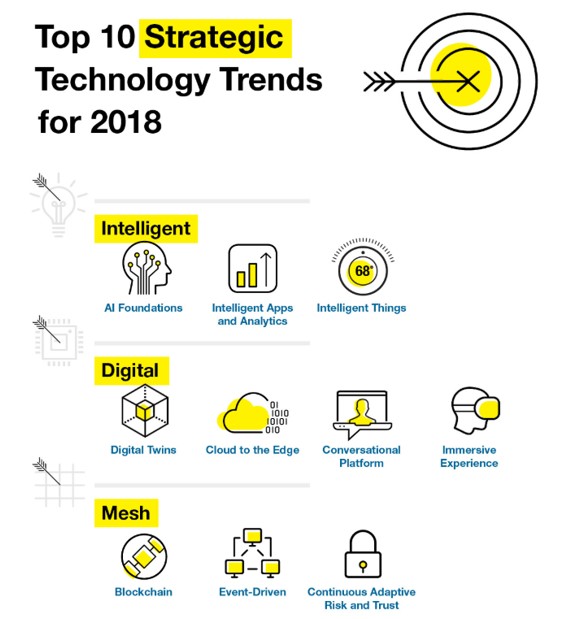
To be fair, the basis of the digital twin technology is not so new anymore. For years, manufacturers have used digital production models that could collect data such as temperature and pressure indications and through them make simulations of their production processes. But what makes digital twins relevant as a concept now is that technology, such as 3D-formated data, has made it possible for the simulations to be even more developed and life like than they were before. Also, the newest technologies make combining different types of simulations possible. Not only can the user simulate the structure and design of the production process but now also the individual processes in production can be simulated for a more accurate digital experience of the real production.
Because of the industry’s interest in digital twins, MADE recently organised an innovation conference where researchers and industry specialists could share their experiences with using this up-and-coming technology in their labs. One of the key takeaways from the conference was how many different purposes the digital twin concept can have. In fact, the digital twin can open the doors to new simulation and testing options that would otherwise we extremely expensive and/or difficult.
You might get the sense that the digital twin is a strictly technical tool, but it turns out the digital twin is also ideal for assistance and service tasks not to mention training and educational purposes and these are just a few of many usages. In line with this discovery which came out of the conference, another interesting point was that digital twins can be used as an organisational tool, since a better description and thereby understanding of production can contribute to get a better shared understanding about your production in the organisation.
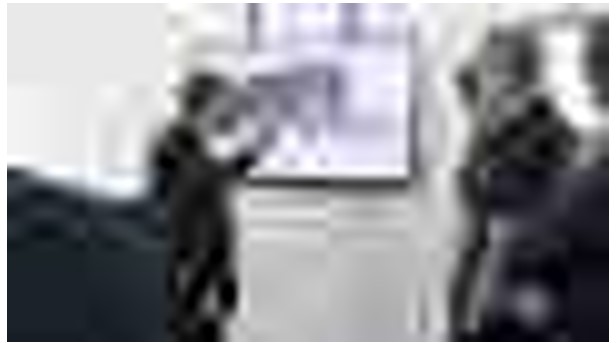
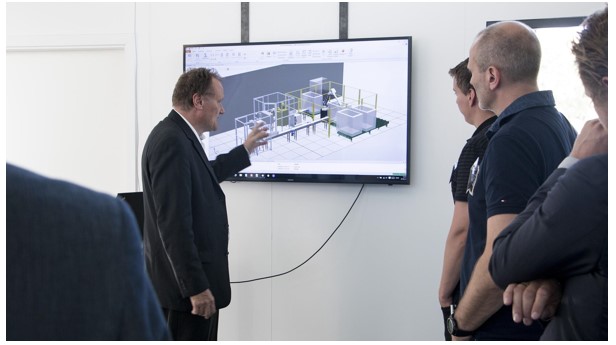
But what about you? Do you agree that digital twins will be a key technology in the future? Have you used digital twins in production and if so, what potential do you see in this technology? Share your thoughts below and join the I4MS Community for further discussion of key trends in manufacturing.