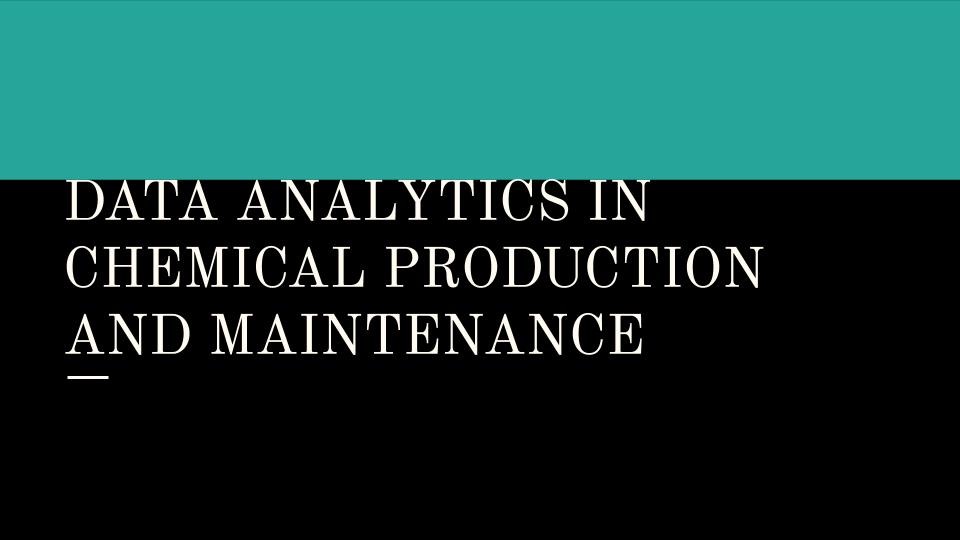
Data is the new oil. The new adage of the new millennium and the future to come will rest on this one premise. Digital has a significant impact on various aspects of the chemical industry. Quite notably, there will be the increases in manufacturing performance to be gained by appropriate data collection, and the associated decision making processes that come along with this. The Chemical manufacturers that have invested heavily in IT systems and data collection infrastructure that collate data, are often the ones who are the most equipped to take advantage of an future that is unfolding. With data, you can control the future of the organization. Information tells you what to do, when to do it and to what market you’ll be best able to partner with.
Computational power is now accessible by all. Organizations now have increased access to better tools that will be able to determine their current operational status, and also help to identify what the path going forward is scheduled to be . With computers, industrial plants can gather information from multiple sources and also take advantage of tools such as machine-learning and visualization platforms to uncover ways to optimize plant operations.
An excerpt from the industrial consultants at McKinsey and Company say it best:
“Advanced analytics can substantially raise the level of understanding of what happens in a chemical plant’s manufacturing operations; this can help chemical companies solve previously impenetrable problems and reveal those that they never knew existed, such as hidden bottlenecks or unprofitable production lines.”
REAL TIME EQUIPMENT OPTIMIZATION
Starting with the voice of the customer, an appropriate system can be built to meet organizational needs. Plants must stay in operation and one of the best ways to do this…is to simply facilitate continuous operations. Start ups and shut downs are expensive and keeping productive is one of the best ways for an organization to minimize these associated costs. Equipment however, doesn’t run indefinitely and organizations must find a way to ensure that they have their equipment in maintenance for a minimal time. Organizations do design their operations to satisfy their customers needs. Depending on whether a product or service is being delivered, it will be in the best interest of the organization to ensure that the system is up and running.
HOW DATA ANALYTICS CAN OPTIMIZE MAINTENANCE
Various factors can affect the operation of an organization. With improper maintenance, any system in focus will not be able to satisfy its customer. Examples of the impact that improper maintenance can have include asset failure. For any production run, the absence of critical equipment due to downtime can impact an organization in various ways, particularly from a financial perspective. A suitable example is the case of an organization that generates its own electricity in order to reduce costs. Power plants usually have units such as boilers and turbines. With each of these systems in operation, the organization will be able to be self-sufficient. If any of these power generation systems are compromised, then the organization will have to purchase power from the grid, which is more expensive than generating their own and defeats the initial purpose.
Preventative Maintenance is the means via which problems such as asset failure can be avoided all together. It is a suitable data analytics tool, that helps industrial plants to stay on top of their equipment operations. With sensors connected to a server, information on equipment performance such as bearing temperatures, hours in operations, and vibrations can be monitored. The critical set points for these items will be entered into the system, and with time, the relevant triggers for maintenance can be achieved via system alerts.
If an organization can foresee a problem, it will be easy for the solution to be implemented. This is the purpose of preventative maintenance. Via utilization of systems such as Industry 4.0 tools and system sensors, the equipment can actually become smarter and inform its operators of approaching failures so that they can be included in the appropriate maintenance plans.
Preventative Maintenance is part of the Reliability Management of an organization. As the name implies, the system implemented ensures that equipment maintenance is on point. Prevention is better than cure, and in a competitive industry, it is always important to ensure that the system can deliver when it says it will. The following example is an outline of how a Preventative Maintenance System can be utilized in ensuring that systems are operating as desired.
Production operating processes utilize pump systems extensively. Depending on an organization, a process system can have as few as ten pumps or hundreds of pumps in operation. Pumps are critical to the transfer of process fluids from one operation to the next. Production systems require certain flows per unit time in order to facilitate the desired production run. Typically, organizations have back up pumps, or back up inventory in order to address certain issues as they arise. Pump inventory includes the standards like packing, the relevant nuts and bolts, and pump impellers.
The challenge with having excess inventory on hand is that it adds to system costs. With a Predictive Maintenance system, the organization can reduce inventory and operate in Just-In-Time state, and save possibly hundreds of thousands of dollars per day. Predictive maintenance systems are smart systems that allow the system to determine beforehand where the possible failures will be.
As an addition to the PFMEA process, once the system failures are identified, their odds are also determined by the system. In turbines for instance, bearings have system links and their temperatures are noted. Once the bearing temperatures are above a certain point, the system will be notified. Reliability engineers will then proceed to analyze the unit and find the root cause. There will be a window within which the team can then order their critical parts and facilitate a planned turbine overhaul, and ensure that the system is producing as it should.
The importance of Predictive Maintenance cannot be stressed. Organizations have utilized these widely in their operations in order to ensure that they are managing their systems as desired. Six Sigma is all about the reduction of wastes, and industry waste and unplanned down time all contribute to organizational waste. In order to reduce these wastes and have a cleaner running system, Industry 4.0 tools are always welcomed. Technology is always needed for any modern production or service facilities management.
A service example of preventative maintenance systems include a hospital preventative management system. Hospitals, as a service provider, also use various technologies in order to sustain their patients. Auxiliary systems are critical to hospital management. These include incinerators, laundry facilities with boilers to ensure that patients and staff have clean clothing as well as the auxiliary equipment that monitors patients and also performs diagnostic functions. Knowing ahead of time, how these systems operate, what their failure modes are, will ensure that the appropriate plans can be implemented to keep the systems up and running.
Organizations can get comfortable, and neglect equipment, leading to unplanned losses. With preventative maintenance, such incidents will be eliminated.