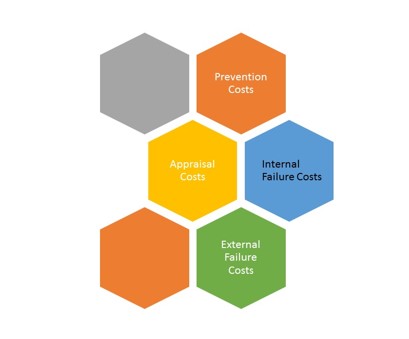
Cost of Poor Quality is a collection of operational losses that is associated with the provision of poor quality products or services. In some instances, the customer will either outright reject the product, leaving the organization to either scrap or rework the product, or will accept the product at a reduced price. Regardless of the outcome, it is not in the best interest of an organization to be losing money, which is why identifying and eliminating the root cause of quality losses will be critical to an organization’s operational improvements.
The Lean Methodology of thinking has identified four major sources of losses in a functioning operational system. These losses will be analyzed below, in this article’s assessments. The cost of poor quality is a lean methodology which measures the impact of these operational losses. Once the opportunity losses are quantized, an organization can then take the steps to reduce the losses according to the order of magnitude. The four types of losses which will be assessed are highlighted below:
Prevention Costs
There is a saying that states that prevention is better than cure. There are some instances where Quality Management System design has built in costs that will ensure that once the system is implemented, downstream losses are avoided. It is the classic case of preparation ahead of the anticipated challenge. Utilizing a system such as ISO 9001: 2008 and the subsequent series is an appropriate means via which prevent costs can be prevented. The system itself, with the built in PDCA cycle, covers all the aspects of Quality Management that are necessary for the system under consideration to thrive.
Appraisal Costs
Lean project management incorporates a monitoring and control phase to ensure that the system under consideration remains in control and capable. Appraisal costs are associated with process management and include procurement assessments, downstream quality assessment along the process, and prior to customer delivery. Critical processes involved in appraisal include the verification processes, Quality Audits (built into ISO) and Supplier ratings via an established procurement system.
Internal Failure Costs
If there’s a system failure, and quality defects are identified…the products or services must be either scrapped or reworked. The costs associated with these two processes account for internal failure costs. Organizations with built in quality systems will usually detect these failures before delivery. As a result systems to facilitate waste, scrap, rework, and failure analysis are the ideal preventative systems to incorporate into the organization’s operations. Prevention is better than cure, so seeing the issue ahead of time, will prevent down stream challenges with the customers.
External Failure Costs
External failure costs occur after the fact. Due to a breach of the quality management system, products can reach the customer in a substandard fashion. Appropriate systems such as repairs and servicing, warranties, complaints systems and product returns work well to ensure that customers are satisfied after the initial disappointment. Most customers are not unreasonable, but the best advice from retail that can apply to all organizations is that the customers must be doubly assured that all will be well, once the breach has occurred.
Cost of poor Quality as an operational loss, cannot be underestimated. In many instances, the costs incurred due to poor quality in one area, can actually span entire supply chains. One very vivid example is in the case of alumina refining. Alumina quality is influenced primarily by the amount of silica in the finished product. Silica, being a glass affects the melting point of aluminum metal once the alumina is fed to smelter pots. If too much silica is present in an alumina batch, the electricity costs of a smelter can skyrocket. In order to protect themselves, smelters will go out of their way to avoid poor quality alumina.
For a refinery who finds themselves in a position where their product is rejected, they could be left with a waiting ship at port. A waiting ship has other locations on their schedule. If they miss their next location, due to waiting on a shipment, an organization will be charged for demurrage. Regardless of the outcome, it is not in the best interest of an organization to be losing money, which is why identifying and eliminating the root cause of quality losses will be critical to an organization’s operational improvements. Applying the Cost of poor Quality Methodology is a sure way to ensure that all remains well with an organization, and good customer-supplier relations are upheld.