A Quality Control Plan specifies the quality controls that are applied to any process or set of processes that have as purpose the realization of a product, be it a service or a tangible product. The Control Plans are not only established in the realization of products, they are also used, for example, in the prevention of occupational risks, in situations related to territorial security, in sanitary safety, or in food safety.
Planning
The importance of planning is crucial, so much so that the professionalism and competence of the managers in any field can be measured according to the plans they are able to establish and, above all, for the efficiency achieved in their execution. Among the different types of plans, control plans occupy a preferential position, as does the Strategic Plan or the Emergency Plans.
Regarding the plans and their execution, said a guru who preferred a bad plan well executed, that a magnificent plan badly executed.
Before entering, it would be necessary to say that it is possible not to use any type of management tool, to completely ignore what a management model is and what
management tools have been developed and work successfully, and yet to grow a business project. These organizations learn by themselves and on the fly, discovering the wheel at every step. Among these, some quickly learn the importance of plans, to think before things, and almost at the same time the importance of communicating the plan to the entire organization, the need to put it in writing. They also see that the most important and most difficult part of the plans is to execute them effectively, from which arises the need to determine the appropriate resources (Human Resources, Infrastructure, and Work Environment, if we look at the structuring of ISO 9001).
Re-Inventing The Wheel
Reinventing the wheel is learning from experience something that is already written or done. As in other technical disciplines there is a scientific support that is univocal and structured, in management we can not find a related figure. The main reason is that we participate in it, the people, endowing the system with a complexity that makes each case unique, although deep down the problems and their solutions are well known. For this reason, organizations are constantly reinventing the wheel.
ISO 9001, in the field of the management of organizations, is laying a foundation of incalculable relevance. Now we are in the phase of which some managers manage to say: here we have an ISO management, as the owner of a company recently told me.
How is a Quality Control Plan made?
The first thing we need to know is that a Quality Control Plan is a final result of a larger process, the process design process. For example, if a company has to manufacture a new product, the Quality Control Plan is established based on the transformation activities of the raw materials in said product. The Quality Control Plan can, and should, determine the way to make the product. Determine, even, how to make the product without it being necessary to control it. At least not in the way we understand control.
We must be clear that the objective is not to control, but to make a product that meets the requirements.
The design of the way to make the product, and the way to control the quality of the product made (defined in the Quality Control Plan), is the design of the product realization process.
Focusing exclusively on the development of the Quality Control Plan, registered as we have said in the process design process, the basic stages that lead to its obtaining are:
1. To define completely what stages the manufacturing (or service provision) comprises, what productive means are going to be used (machines and tools), what raw materials, how many people and what competence they must have, what work procedures will be used, what legal and regulatory aspects affect, what are the requirements of the product, etc.
In practice, a large part of this information is usually determined graphically in a document called a process synoptic (also known as the process flow diagram and other variants). The synoptic of the process structures the work field in stages, which will be used throughout the design process of the control plan. As indicated above, the design of the plan can modify the way of working and / or enrich it. With which it will modify and / or add new elements to the synoptic.
2. Analyze the risks associated with the performance of each of the determined stages. Commonly known as FMEA (Analysis of the Mode of Failure and its Effects), this analysis evaluates and scores each of the risks associated with manufacturing or service provision according to its severity, occurrence (the probability of occurrence), and detection (probability that the problem is detected when it appears), to obtain, product of the three, an index called Risk Priority Index.
A Quality Control Plan aims to guarantee that the resulting product meets the requirements. To achieve this end, it seems logical that we analyze first what can go wrong, what can fail. FMEA is nothing more than a structured technique to highlight the weak points of the process and obtain a weighting of these risks.
The FMEA is made based on the process of realization of the designed product, including quality controls that may already exist. This technique is not only applied to processes, it is also common to apply it to productive means and product design. In an FMEA, we must assess each identified risk assigning a note in the 3 most relevant factors: Gravity, Occurrence, and Detection. The assignment of the grade should be as objective as possible, and for this purpose some criteria to assign scores are set.
The factors subject to valuation are complementary to each other, and have the same importance in the final result, since in the end the product of the 3 is calculated.
The most common is to assign scores of 1 to 10 in each factor, with which the calculated index is a number between 1 and 1000.
Where the Control Plan is actually designed is during the realization of the FMEA. The organization can set the level of risk from which to introduce controls or modify process elements that reduce it. As already warned, to reduce the level of a risk, our actions may have the following effect:
a. Decrease the severity of the risk.
b. Decrease the likelihood of it happening, or
c. Increase detection capacity.
Acting on any of these factors decreases the level of risk. In the automotive sector, a fairly widespread practice is to set the level of risk accepted in 100.
Any risk that obtains a higher grade must be reduced by introducing some change or additional control in the process.
3. Document the Control Plan. If we have done correctly the previous stages, we will have all the necessary information to do it. The aim is to document at least the following:
a. Specify stage by stage of the product realization what characteristics the product must meet, with what productive means it is transformed, and what variables are controlled and how.
b. Specify quality controls performed by laboratories. Tests on raw materials, semi-processed products, or on the final product.
c. Specify the product or process audits that will be performed.
The control plan can directly contain this information, or refer to the documents that contain it: plans, raw material technical sheets, work instructions, defect panels, self-control guidelines, etc.
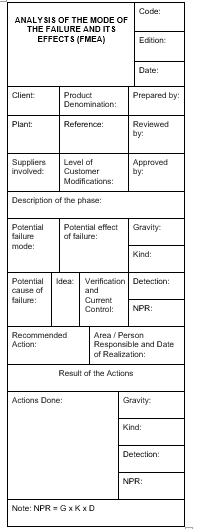