A Six Sigma method of identifying and addressing process lag.
If they are wise, every organization goes through rigorous testing steps to smooth out kinks in the production process. Disruptions in and hindrances to ideal production levels exist in the form of delays, human errors, machine errors, defects, and more. It is wise to have not only a testing phase in place, but also a response plan of action.
The Control Plan phase of Six Sigma narrows in on production disruptions. It is designed to identify where lags or errors in the production process exist and to lay out how an organization is to respond to these lags–whether that be a corrective action, the reworking of a product, or scrapping a product.
Control Plan
The Control Plan phase of Six Sigma is a later phase and it is actually one of the simplest–or most straightforward–parts of the overall system. It is also one of the most critical. Identifying problems in production early on is one of the greatest ways to avoid unexpected disasters that could lead to slowdowns, PR embarrassment, and, of course, loss of company profits. However, once problems are identified and corrected, it is also critical to have an ongoing process in place that ensures that these corrections are sustained. This is done via ongoing quality control–ongoing monitoring of processes and a written plan of corrective action.
So how does Control Plan work? Usually, an organization utilizing Six Sigma will have a visual layout for the Control Plan phase. This layout consists of the various steps in production, description of problem possibilities, and pre-planned reactions to those problems should they occur. It states what quality control measures should be applied in various situations.
Control Plan templates and layouts often vary quite a bit from organization to organization. We focus here on a model that is somewhat general but widely-applicable using a manufacturer of simple wooden toy cars, Acme Toys, Inc, as our model:
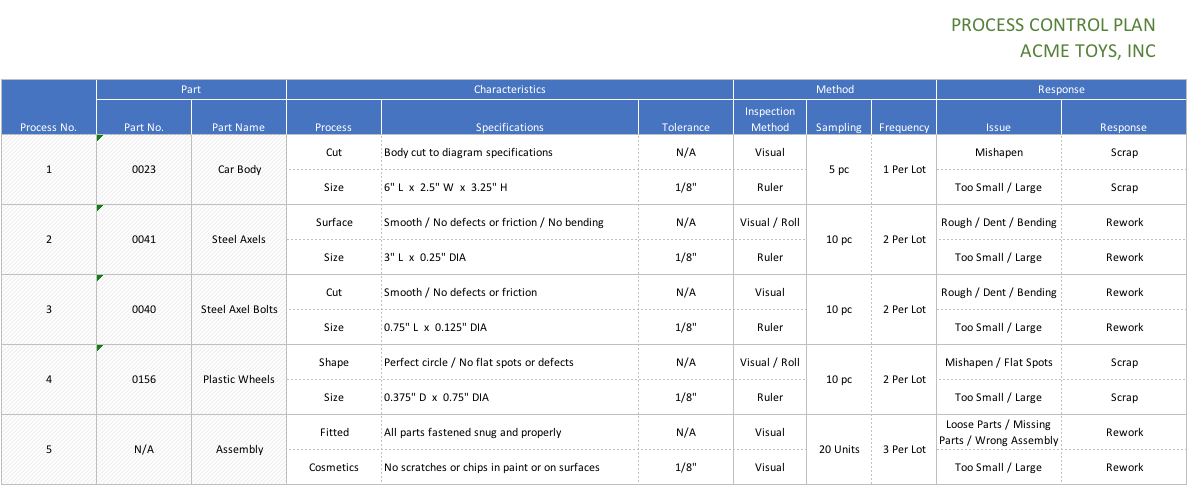
Now we will describe the purpose of each column in the above Control Plan:
The Process No. column lists the step in the production process, then proceeds to the right with the inspection steps and methods. Under the Part heading, the Part No. and Part Name columns list the technical part number and describe the particular part being inspected.
Under the Characteristics heading, the Process column lists the specific characteristic of each part being inspected, followed by the Specifications column that defines specific standards that the inspector is to look for. For example, each car body is cut from a block of pine wood and inspected for accurate shape and proportions as compared to a printed diagram. They are also inspected for overall size. The length must be 6”, the width 2.5”, and the height 3.25.” Lastly under characteristics, the Tolerance column states how much variation from the specifications is allowed. For example, the car body will be approved for shipping only if it is 6” long, give or take 0.125” or, in other words, 5.875” up to 6.125.”
Next, the Method of inspection is defined. Inspection Method defines exactly how each part is inspected. For example, plastic wheels are inspected visually for defects and physically rolled to ensure they are uniform and that there are no flat spots. Sampling defines how many parts are inspected at a time. For example, car bodies are inspected in sets of five while steel axels are inspected in sets of ten. Frequency instructs the inspectors as to how many times to inspect each part or how many people must perform an inspection. For example, steel axels must be inspected twice each–twice by one inspector or once by two inspectors.
Lastly, the planned Response to each discovered issue is listed. The Issue column defines varying problems that might be found for each part, directing the inspector to the next column, Response, to determine what to do with the defective part. For example, if a steel axel comes to the inspector bent, it is sent back to be reworked (the steel is melted down and used to remake the part). A plastic wheel with flat spots is scrapped entirely. If a finished unit (toy car) comes through with loose parts, such as axel bolts that have not been properly tightened, the unit is sent back to assembly to be reworked.
This layout is not all-inclusive. Many organizations list many more possible issues for each of their steps. Others might include a column to list what resources are used for inspection such as machinery, magnifying glasses, etc. But this layout should give you a general idea of the concept and end goal of the Control Process.
In Closing
We are sure that you can see why the Control Plan process is so critical, even though it is simple. It is not enough to correct production issues once and forget about them. Ongoing monitoring and adjustments where necessary are just as important. Should you wish to learn more, a good search of the web for control plan templates will provide quite a few examples of how different companies and consulting firms approach this great system of quality control.