The APQP Manual offers general guidelines to ensure that Advanced Product Quality Planning is implemented according to the specific requirements of the clients. It does not offer specific instructions on how to get to each entry of the Control Plans, a task that is best left to each organization. Even when it is intended that these guidelines cover all situations that normally occur at the beginning of the planning phases, design phase or process analysis, there will be questions to be generated. These questions should be directed to your authorized customer representative.
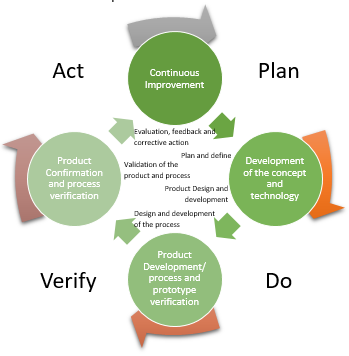
The following are the important guidelines detailed in an APQP Manual:
Planning and Definition of the Program
It is necessary to determine the expectations and needs of the clients in order to plan and define a quality program. The initial step of the process of quality planning of a product is to ensure that the needs and expectations of customers are clearly addressed.
Understand Customer Needs
This Is done using the voice of customer techniques to determine customer needs and with the deployment of quality function to organize those needs and translate them to the product features/required.
The “Voice of the Client”: This is the term to describe the needs or requirements stated and not specified by customer. Customer’s tin voice captured in a variety of ways: direct discussion or interview, exam, main group, customer specification, observation, warranty data, field reports, etc.
Capturing the Client’s Voice
Once a product plan that defines the target market and customer is established, the next step is to plan how to capture these customer needs from each development project. This includes determining how to identify customers to get in touch to capture what they need, what mechanisms they should use to pick up their needs, and a schedule and resource estimate to capture the customer’s voice (project plan for the product definition phase).
Deployment of Quality Functions (DQF) is a structured approach to defining customer needs and requirements and translating them into specific plans to produce products to meet those needs. The “Voice of the customer” is the term to describe these stated and needs or requirements without specifying customer.
The client’s voice is captured in a variety of ways: direct or interview, exam, main group, specific customer, observation, warranty data, etc. This understanding of customer needs is then summarized in a product planning matrix or a “quality house”. These matrices are used to translate a higher level “what is” or need in lower level product requirements “How is” – or technical characteristics to meet these needs.
While the Quality Function Deployment matrices are a good communication tool at every step in the process, the matrices are the means and not the end. True value is in the process of communicating and decision making with DQF.
DQF is oriented towards the participation of a team of people representing several functional departments that have involvement in product development: Marketing, Design engineering, quality assurance, Manufacturing/Manufacturing Engineering, test engineering, finance, product support, etc.
Product Design and Development
The Product Quality Planning Team should consider all design factors in the planning process and when the design is owned or shared by the customer. The steps include manufacturing prototypes to verify that the product or service meets the customer’s voice objectives. A feasible design must enable compliance with production volumes and programs and be consistent with the ability to meet engineering confirmities, along with quality objectives, reliability, investment cost, weight, unit cost, and scheme of time. Although feasibility studies and control plans are primarily based on engineering drawings and specification requirements, valuable information from analytical tools described in this chapter may be derived for later Define and prioritize features that may require special product controls and process.
Product and Process Validation
Validation of the selected manufacturing process and its control mechanisms with the evaluation of production performance contouring the mandatory conditions and production requirements identifying the outputs required.
Feedback, Evaluation and Corrective Action
Quality planning does not end with the installation and validation of the process. It Is at the stage of the manufacturing of the components when the results can be assessed and where all common and special causes of variation are present. This is also the time to evaluate the effectiveness of efforts in the quality planning of a product. The Production Control plan is the basis for evaluating the product or service at this stage. Variables and attributes data must be evaluated.
Appropriate actions Should Be taken as described in the Reference Manual for the Process Statistical Control of Chrysler, Ford and General Motors. Organizations that fully implement an effective APQP process will be in a better position to meet customer requirements, including any special features specified by customers.
Control the Methodology of the Plan
The purpose of this control plan methodology is to assist in the manufacture of quality products and in accordance with customer requirements. Makes a structured approach to the design, selection and implementation of control methods and value added for the total system. The Control Plans provide a written and summarized description of the systems used in minimizing the variation of products and processes. The Control Plan does not replace the information contained in the operator’s detailed instructions. This methodology applies to a wide range of manufacturing processes and technologies.
The Control Plan is maintained and used throughout the life-cycle of the product. At the beginning and in the life cycle of the product, its main purpose is to document and communicate the initial plan to control the process. Subsequently, it offers a guide to manufacturing in how to control the process and ensure the quality of the product. Finally, the Control Plan is maintained as a living document that reflects the current control methods and measurement systems used.
The Control Plan is updated as the measurement systems and control methods are evaluated and improved.