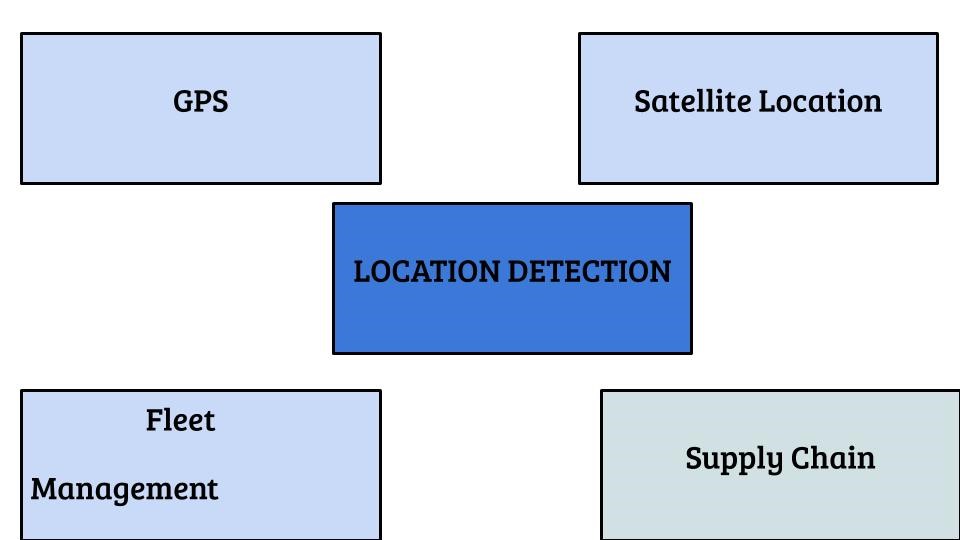
“Just like a GPS, the universe sends you signs to show you the best course. If you follow the flow, you get where you want with ease and happiness. If you miss a turn, the road becomes longer and harder.” ― Charbel Tadros
An industrial plant comes alive, when the integration of various items such as sensors is utilized to generate critical plant information. In industrial process control, there is an initial need to see or feel the plant from one control site, without actually having to walk the field or be in front of the equipment. Let us utilize a chemical plant as our general example in this instance. Chemical plants are in the business of processing raw materials into finished goods for delivery to customers.
A chemical plant is very complicated, with each department having hundreds or even thousands of components that are linked together in a sequential flow. Operating staff do not have the ability to monitor all equipment at once. Having to physically walk the plant can be an exhausting activity, but via TDC systems, and even the advent of VPN, control engineers and process engineers can read their systems from the comfort of any location with an internet connection. The plant, once activated with appropriate sensor networks, will tell you when there’s an issue.
With a process control system, a visual layout of the process from varying dimensions can be accessed. The first step to an appropriate process control system is having field sensors. These types sensors include:
Flow Sensors: These sensors are variable in design, but at the baseline, they are designed to capture the flow of anything from air flow to slurry flow.
Pressure Sensor: These are critical for vessels that need to remain at appropriate pressures in order to facilitate critical operating conditions. In the alumina industry for instance, alumina digesters have to operate at pressure, because the temperatures reached in the heater system will be enough to vaporize the sodium hydroxide extracting solution. At high pressures, the digester vessels keep the liquid in liquid phase. To ensure appropriate system performance, critical internal pressures will be tracked by a pressure sensor on each unit.
Temperature Sensor: Another critical tool that is utilized on industrial sites is a temperature sensor. Chemical processes, biological processes and even some physical systems such as rockets, do require that critical temperatures be monitored. In a chemical process temperature is key to appropriate reaction rates. In a biological process such as a cell culturing, temperatures for appropriate incubation will be necessary. Additionally for physical systems such as cars, internal temperature monitoring will be key to ensuring that the engine is performing to par.
Sensors that are connected to the central control system will provide a feel for how a system is moving. With the central operating plant however, there are individual components that are actually moving through the system and will need to be tracked in order to determine its motion through a system as it flows from supplier to customer. Just like the advent of the stationary sensor above, there is the advent of sensor technology that can track moving components in a system, and also the location of moving individuals.
Throughout warehouses, supply chains and delivery systems there will be a multitude of devices that can be utilized. These include tablets, laptops, cellular phones and also smart watches. Location detection technologies, via the advent of the Global Positioning System, are able to identify utilizing critical technology where critical items are. As a fleet is moving through a delivery system for instance, customers can phone in, or even track via the online system, where exactly their items are in the delivery process. Are the items:
- In the warehouse waiting to be loaded
- Enroute to delivery
- Delivered and signed for
All of this information is usually readily available. For civilians, the best delivery tracking system that is relatable to is Amazon’s delivery system. If you order an item online, via a tracking mechanism, you are able to identify where your item is on the delivery chain. Likewise, for all industrial products, sensors make traceability possible for various reasons including quality and safety. In those instances where products have to be recalled, bar coding or the use of RFID tags that are easily traceable via scanning devices is a tool that supply chain managers utilize to ensure that they are able to keep track of all their product dispersions.
Satellites, sensors and the critical data transmitted via location detection is a means that industrial sites can maintain traceability of their products through a system. ISO 9001 as a system, has a requirement for recall and identification of bad products. Location systems were predominantly designed to satisfy requirements such as these. With an appropriate Location Detection system, various aspects of your operational management will be readily manageable.