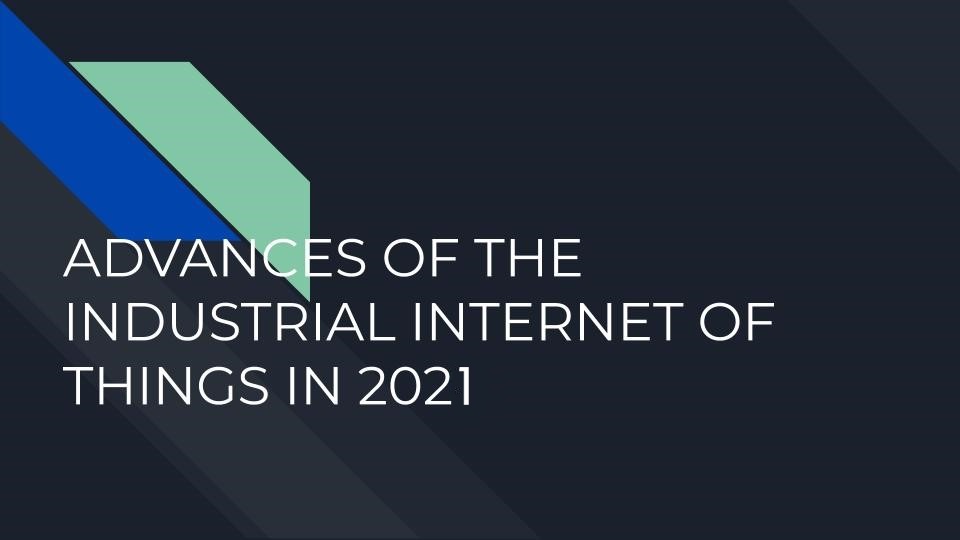
“Any approach to strategy quickly encounters a conflict between corporate objectives and corporate capabilities. Attempting the impossible is not a good strategy. It is just a waste of resources.” – Bruce Henderson
Industry 4.0, represented by the Industrial Internet of Things is an interesting and exciting aspect of process engineering that we all must embrace. In a time like this…with the advent of a pandemic, a smart factory can practically run itself, unless there’s some deep underlying issue such as a process leak. In the production realm, embracing technology and optimizing industrial systems will only bring them to their full potential. This isn’t the rise of the machines, it’s simply an age that will enable higher quality products to be generated via the advent of technology.
The world is always growing and changing and evolving due to its dynamic nature. The interconnection of various smart devices to form a smart space is known as the Internet of Things. Likewise in the industrial realm, the interconnection of all devices in an industrial process flow is identified as the industrial internet of things. A smart factory is the wave of the future. If you thought your current factory was smart now, there’s still always room to make it much smarter and to automate it further. The limit does not exist.
As a grand vision, the plant will eventually require minimal intervention in order to accomplish its objectives. Knowing that humans are flawed, via the advent of the industrial version of the Internet of Things. Known as the Industrial Internet of Things, sequential process systems via their interlinked software and sensor networks can actually interact with each other and auto adjust when needs be. Continuous industrial processes have master control loops that monitor critical process parameters across the entire circuit.
ADVANTAGE OF THE INDUSTRIAL INTERNET OF THINGS
With the vision for the Industrial Internet of Things outlined, let us now set a baseline for what the advantages of such systems are:
- Improved data access: The advent of the Industrial Internet of Things has transformed the way that plants are operated globally. A process engineer can practically just log into a plant facility from the comfort of their VPN, and see what the process is doing. If there’s an issue, they can simply call into their respective control room, and give the relevant process instructions that will ensure that the process is performing as it should.
- Improved process agility: With processes rapidly changing in some sectors, it will be important for manufacturers to be agile in order to be competitive. With the data from the collective sensor network in the factory, operations managers can identify with speed what products the factory will be outputting.
With the Industrial Internet of Things or IIOT, the digital interconnectivity in a plant is such that when applied to manufacturing operations, the payoffs are quite great. With the appropriate sensor-actuator fusions in a plant, smart machines and real time data analytics will champion your organization to its next frontiers. Critical elements in your plant will include:
- Smart machines with sensor-software combinations that enable information processing and quick decision making.
- Cloud computing to collate, and store the expansive data that is collected per second in a processing operation.
- Data analytics systems that will enable data mining for your process.
Benefits of IIoT
2021 is expected to bring the value of IIOT related items to about 100 billion dollars. Knowing that the value of your industrial property will increase what can you expect as a process owner?
-
Efficiency! Efficiency! Efficiency!
The reason that all engineers exist is to make process systems better and more efficient. You can expect increases in your process efficiency for with the IIOT, because you can see everything. Knowing the capability and control of your process will enable you to ensure that all the critical peaks and troughs of your process are handled automatically.
With interconnected process units, entire unit operations as well as individual sub unit performance can be assessed by your process data. As a manufacturer wanting to squeeze every ounce of performance on your system, you’ll be able to determine where your improvement resources should go.
-
Error Reduction
Humans are flawed, and while robots won’t run forever, they do have the ability to replicate tasks in a uniform manner for the duration of their operational time. Reducing errors in an industrial plant is the key to quality control, which will bring us customer satisfaction.
As the world becomes more automated, industrial automation is by no means left out of the loop, they are opportunities still to be gleaned from this. Just as with all industrial operations, before implementing, simply go through with your process team, work through a problem solving A3 and you’ll be able to calculate the gains prior to implementation. With a thorough business case, you’ll be able to pull your organization to higher heights. Keep Optimizing!!