Methods for Getting to the Root Cause of a Problem
It is important to exercise the process of root-cause analysis–that is, when an issue in business occurs, to take the time to not only identify and fix the immediate issue but dig deep to find out why it happened in the first place. Six Sigma suggests a common-sense practice for doing this called The 5 Whys. You can download the template at the bottom of this article, but first an explanation…
What Is the Five-Whys Process?
The Five Whys process is repetitive by definition–but in a good way. Upon hearing it explained, it may sound robotic, but it is useful to be sure. It is as simple as this:
When a problem arises in business, seek to prevent the same issue from happening again. To do this, ask why things happened over and over until you reach the root of the problem.
In short, we ask, “why,” over and over until we reach the root cause. Typically, you will find the root cause by the time you’ve asked, “why,” five times.
For example, we looked at a small bakery in the article on stability control charts. In that example, the bakery experienced a lag in production where crescent rolls took way longer on average to produce for a period of three hours. It was discovered that an oven’s electrical wiring had a short that caused a heating element to sometimes turn on and other times to not turn on. In order to discover why crescent rolls would sometimes take much longer to be produced (the problem), they asked a series of “why” questions. It probably looked something like this:
-
Why are crescent rolls sometimes taking longer?
Because the oven sometimes does not heat up to full heat. -
Why is the oven not properly heating?
Because a heating element sometimes works and sometimes doesn’t. -
Why is the heating element failing?
Because there is a short in the wiring. -
Why is there a short in the wiring?
Because it is past its replacement date. -
Why is it past its replacement date?
Because there is no maintenance schedule in place.
By going through this process, they are now able to not only address the malfunctioning oven but address the reason it malfunctioned in the first place.
A simplified view of this process can be placed in a simple, commonly-used flowchart-like diagram:
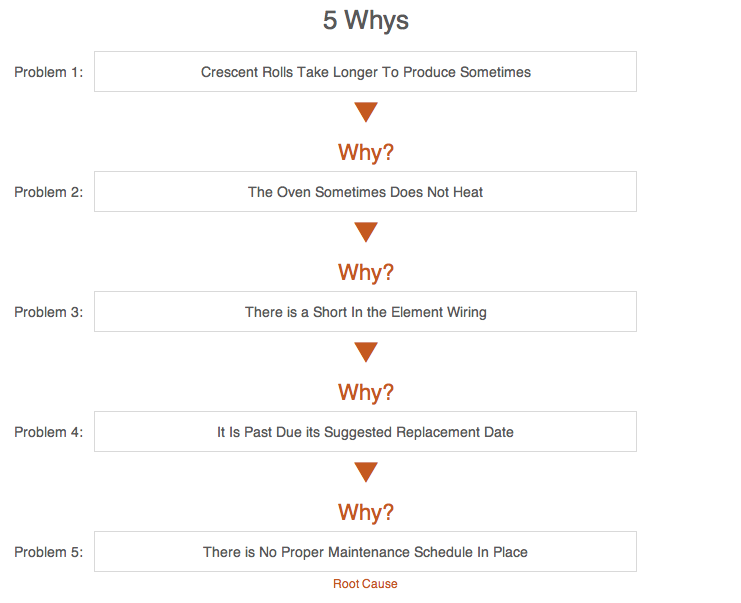
Fishbone Diagram
Another helpful diagram that comes next in the process is called a fishbone diagram. This diagram takes on the form of a fish with the main problem at the head. Working backwards, various contributors to the problem are listed under various common categories of causes.
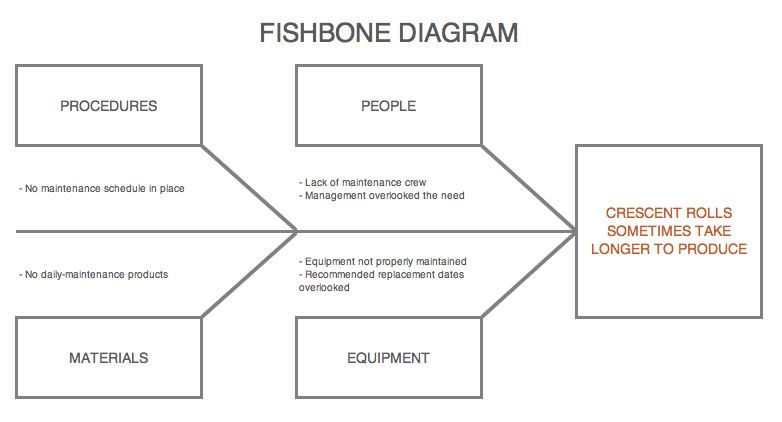
People: This category of cause lists issues related to people such as lack of training or knowledge, oversights, work overload, ethical issues, being short of staff, and more.
In this case, the bakery’s people issues are being short on staff (or hired contractors to perform routine and major maintenance. This situation is the cause of management not being mindful of the need for maintenance and not paying attention to equipment manuals that provide guidance on maintaining equipment.
Equipment: This category of cause lists issues related to equipment that is vital to operation such as equipment failure, defects, effects of depreciation, damage, and more.
The bakery’s equipment issues have to do with neglect–failure to provide upkeep, and parts being used past their recommended replacement dates.
Procedures: This category of cause lists issues related to specific processes (or failed processes) that contributed to the main problem. This can be lag in production, holes in quality assurance, roles not fulfilled, and more.
The bakery’s procedure (or process) issues have to do with a process missing altogether. Had a routine maintenance process been in place, recommended rewiring would have taken place, the heating element would have remained operational, production would not have been stalled by this issue, and customers would not have been disappointed.
Materials: This category of cause lists issues related to materials needed for operation such as missing parts or supplies, defective parts, incorrect materials, and more.
The bakery’s issues do not lie primarily in this category. However, it was also discovered during this analysis that there is daily upkeep that should have been done by the crew to lessen the chances of failure such as scrubbing, changing a simple heat guard that protects the electrical components from the intense heat, and emptying the tray beneath the grates to help prevent buildup of hot char.
In Closing
This process, of course, is not absolute. It is not guaranteed, of course, that the root cause of every complex problem can be discovered after asking, “why,” five times. There are so many issues with so many factors that no one could possibly foresee them all. However, there is a high likelihood that you’ll have a pretty good idea of what the root cause of an issue is after asking, “why,” around five times.