Six Sigma is known for its systematic and quantitative analysis that bases its study on given data. The purpose of the analysis is to improve the efficiency and productivity in the organization. Any improvement done whether on the process or the product/service eventually leads to more satisfied customers, which means more profit.
Several Six Sigma Tools have been discussed; each of them has its own characteristics, advantages, and disadvantages. Mistake Proofing is another Six Sigma tool most of the time integrated with other Lean Six Sigma Tools such as 5S Visual Management, Quick Changeover, Standard Work, and One Piece Flow. Sometimes called Poka-Yoke or Fail-Safing, it is characterized as an improvement procedure (or device) which aims to avoid or eliminate defects or errors from happening.
The procedure is capable of immediately detecting errors once they occurred. The procedure implements correct operations by getting rid of choices which may lead to wrong actions. The potential of Mistake Proofing is endless and requires little resources.
When to use Mistake Proofing
Not all Six Sigma studies require the use of Mistake Proofing. Though the procedure does not require much funding, the study involves lots of work which equates to more time. Mistake Proofing is suggested when the consequences of a defect are costly or bear high risk. It is also conducted when a minor defect which is detected in the early process will cause major tribulations in the later process.
All service-oriented studies are encouraged to use Mistake Proofing. This is because customers can create defects which will eventually affect the output. Some organizational processes involve human interventions. These interventions can cause defects – that’s why Mistake Proofing is also encouraged for processes that rely on worker’s skill, attention or experience.
Lastly, Mistake Proofing is also recommended for hand-off processes. This is the process when a customer is transferred to other personnel. The situation will identify the reaction of the customer if he/she will be transferred to another personnel.
Advantages of using the Mistake Proofing method
Since the aim of the study is to detect possible mistakes or errors, it possesses several advantages not just to the study and the organization but to the team as well:
- Encourages individual accountability for excellence.
- Without involving too much effort, the procedure performs 100% assessment.
- Discovers and eradicates defects as early as possible in the process.
- Presents immediate response, thus minimizing the time for remedial action.
- Creates a process of consecutive verification for each procedure.
- Presents self-check actions which provide quicker review than consecutive verification.
- Makes sure that proper circumstances exist before the actual creation, and prevents defects from taking place.
- Doesn’t just identify the causes of errors but eliminates the causes as well.
- Elimination of defects ultimately increases customer satisfaction.
- The focal point is on waste reduction in defects and processing.
The 5 Causes of Errors
To be able to create and conduct an effective Mistake Proofing campaign, it is essential to understand the common causes why these errors occur in the first place. Knowing the reasons not only lessens the time spent on creating action plans but it will also help identify what and which actions to take to immediately determine mistakes. Generally, there are five reasons why mistakes or errors occur:
- Current processes are unreal and incorrect. The reason could be either the environment, it does not fit the job, the materials, the equipment, the labor resources, or the measurements.
- Variation in the process is too much and unnecessary.
- The variation in raw materials is disproportionate.
- The measuring device used is not accurate.
- Incidence of human mistake or error.
Human Error
There are several factors contributing to human error. To name a few – multiple tasking, adjustments, lack of standards, infrequent tasks, and redundancy that is too hurried for the employee. The incidence of human mistake or error can be further explained or grouped into ten sub-categories:
- Poor memory or not focused
- Misapprehension or making conclusions even if the information is not complete
- Classification or seeing the circumstances incorrectly
- Training, either incorrect training, or lack of training, or no training at all
- Willful mistakes where people deliberately ignore the regulations
- Unintentional mistakes or errors relating to fatigue or distraction
- Decision impediment
- Deficient in set of standards
- Unplanned incidence, and
- Other premeditated errors like sabotage
Mistake Proofing procedure
To assure favorable results of Mistake Proofing, certain procedure should be followed. Similar to all other Six Sigma tools, procedures will vary depending on the scope of the study. Mistake Proofing procedures for a sales process study are different from that of a manufacturing process. Below is the general guide for conducting Mistake Proofing. Keep in mind that Mistake Proofing aims to immediately identify defects so it could eliminate possible mistakes, so the procedure should focus on every avenue where human intervention is possible.
- Construct a flowchart of the whole process. Review every step and think about when and where human mistakes are most expected to happen.
- For every possible mistake, look back throughout the process and find its possible source(s).
- For every defect, think of probable means to make the mistake impossible to happen. Consider means such as:
- Replacement – substituting the step with an defect-proof step
- Elimination – getting rid of the step that causes the defect
- Facilitation – making the right action simpler than the mistake
- If it is unfeasible for the mistake to happen, think of means to discover the mistake and reduce its consequences. You could use other procedures such as setting function, inspection method, and regulatory function.
- Select the preeminent Mistake Proofing procedure or method for every mistake. Evaluate it then execute it.
Determining the error
There are three ways to determine the error and reduce its consequences – setting function, inspection method, and regulatory function.
There are three types of inspection methods that give quick reviews:
- Self-inspection is a process where employees evaluate their own work instantaneously after doing it.
- Successive checking is done at the successive step and conducted by the next employee.
- Source checking is done prior to the process step and conditions are right. Most of the time it is a routine and keeps the method from continuing until all conditions are correct.
Checking the product feature or process parameter possible errors is a method called setting function:
- Physical or contact method inspects the physical feature such as temperature and diameter.
- The sequencing method also called motion-step approach checks the process series to assure that steps are done accordingly
- Counting and grouping method also known as the fixed-value approach counts the number of repetitions or weighs or parts of a product to guarantee completeness.
- Information enhancement, though required in all processes, ensures that information is accessible and perceivable whenever and wherever required.
Regulatory functions on the other hand are signs that alert the employees that an error has happened:
- There are several warning functions such as lights, buzzers, bells, and other sensory alert devices. You can also consider the use of symbols, shapes, color-coding, and other distinctive sounds.
- A control function avoids the procedure from taking place until the mistake is properly corrected or conditions are accordingly corrected.
Putting it all to work
Mistake Proofing can utilize either a table or a flowchart depending on the scope of the process and objective of the analysis. A flowchart is recommended if the objective is to identify the frequency of human intervention and when and where in the specific process can an error happen. This is effective because it creates possible scenarios of every step. Tables on the other hand are used to determine the effects of an error and how it can be resolved. It indicates specific action for every error level. Examples are posted below for better understanding.
The Mistake Proofing table below illustrates the level of mistake or error in column one. Identified levels vary depending on severity of the error and its effect to the process or product. The Action column illustrates that specific action corresponds to specific levels. Prompt column shows the trigger which is essential to determine the severity of each level. This answers the question on urgency of action – should we stop the process or can the process still handle the error?
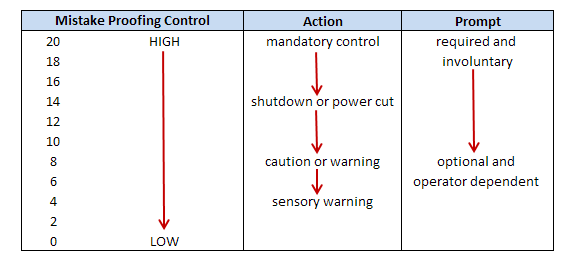
Mistake Proofing Table
To illustrate Mistake Proofing using a flowchart let us use a salon as an example. The case is that the shop is thinking on how to increase their low client turn out. Below is the usual service flow of the said salon. The salon is a service oriented business therefore there a lot of avenues where an error may occur. Errors or mistakes can be caused by either employees or customers. The goal of Mistake Proofing is to identify these potential errors to prevent defects from happening.
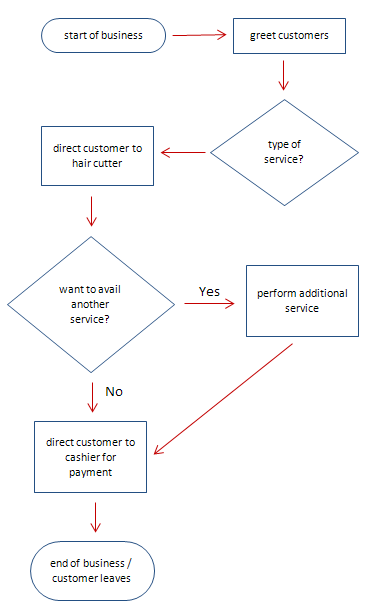
Mistake Proofing Flowchart Example
A possible error may occur as soon as the customer enters the salon. It could be a displeased customer because he or she was not immediately greeted by the staff or the staff was not there to welcome them. To address this possible error using Mistake Proofing, the salon can install an electronic sensor or hang a bell to signal the staff that someone had entered the shop. Another Mistake Proofing solution is to assign a staff whose job is to welcome the customers.
Potential errors caused by employees may happen every step of the service process. From asking what salon service the customer wanted, doing the service, asking if the customer wanted additional salon service or wants to avail their promotion, securing payment, and up to the time the customer leaves the salon. Every step should be considered and all possibilities should be studied to be able to come up with solutions that will prevent further defects.
A possible error on the part of the customer is that when they are greeted and asked what kind of salon service they wanted, they would not understand this question if there is loud noise produced either by people inside the salon or music from an audio player. A Mistake Proofing method that aims to prevent this from happening is to ensure that music inside the shop should be in minimal volume so it will not cause distraction to other people. Staff should also be trained to use audible not loud voice when conversing with their customers. Setting of rules such as no horse-play, no distractive conversations amongst staff is also an example.
To sum it all up
The Mistake Proofing technique does not only eliminate errors caused by customers but it also improves the environment of the salon by eliminating exasperating loud noises. Assigning a receptionist to greet customers sends a message that they are valued the moment they enter the salon. Take note that being a service oriented business the focus should always be on how the customer would react to specific situations. The work of Mistake Proofing is to anticipate potential errors and create steps that will prevent these errors from happening.
Increasing customer turnout begins with providing exceptional customer experience. The result may not be as quick as desired but the assurance that the customer leaves the salon bearing a smile is a positive thing.
The customer can always choose to return to the salon or go to another salon. The factors that will make the customer return to the salon are in the hands of the staff and the salon management. Customers are the cheapest form of advertisement. They can increase turnout by referring their family members and friends to the salon. The important thing is that they should be delighted and not just satisfied with the service.
Mistake Proofing is one effective tool that can improve organizational processes, service, and products. Its ability to spot errors has been long proven and several companies have attested to this. Buzzers, signals, alerts, sensors are just few samples that can improve the level of service and process. It will all depend on the project owners to assess the situation and recommend solutions. That is why it is best to use flowcharts and tables to easily identify factors or areas than can cause errors.