Jidoka is also a Japanese term which means ‘Autonomation’. No it is not simply ‘Automation’. It is ‘Autonomation’. Autonomation means ‘Automation with human touch’. Jidoka is one of the three pillars of the world famous ‘Toyota Production system’ and also a key concept in ‘Lean Manufacturing’.
The concept of Jidoka is “Automatic detection of problems or defects at an early stage and proceed with the production only after resolving the problem at its root cause”. This means, the machines and operation will stop automatically without any human intervention or supervision, once a problem is detected or a defect is found.
Originally, this concept was first used in 1896 by Saichi Toyoda. He first invented a textile loom that would stop automatically when it comes across a defective thread. This seemed to be very useful in terms of: Time, Quality & Cost.
How does Jidoka do this?
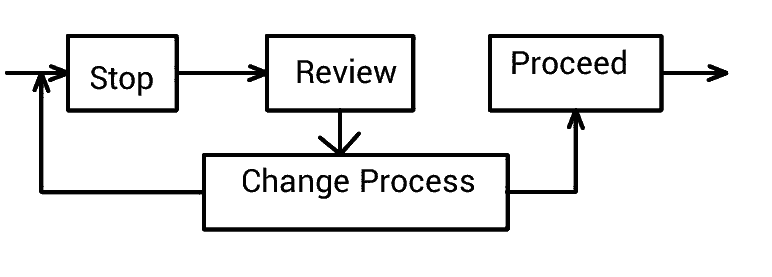
- By implementing ‘Jidoka’ or ‘Autonomation’, the human intervention and supervision to detect and identify defective units or defects get considerably reduced. This is a direct cost saving, and companies can also use this manpower for more productive work.
- The production stops when a machine detects a bad product and resumes only after correction of the root cause of the problem. This improves the quality of the products in first hand, and improves the efficiency of the production system also.
- The problems and defects are identified and resolved then and there rather than accumulating the errors till the end of production line. This saves a huge amount of rework, inspection time, time and effort of the labor and helps in early delivery of goods, in turn the adherence to the cycle time.
- Correction and Prevention of errors during production cycle itself, restricts the defective units to reach the customer and hence reduces dissatisfaction, and wins customer confidence.